Common Production Processes for Battery Holder Materials
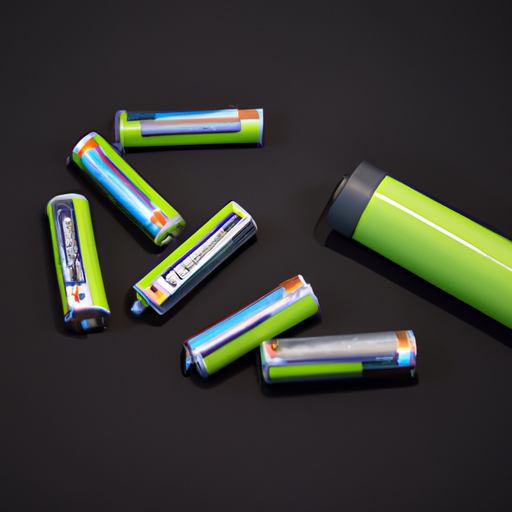
I. Introduction
Battery holders are essential components in a wide range of electronic devices, from remote controls to sophisticated medical equipment. They serve as the interface between the battery and the device, ensuring a secure connection that allows for efficient power transfer. The importance of battery holders cannot be overstated, as they play a critical role in the overall performance and reliability of electronic systems.
Battery holders are made from various materials, each chosen for its specific properties, such as durability, conductivity, and resistance to environmental factors. Understanding the common production processes for these materials is crucial for manufacturers aiming to optimize performance and reduce costs.
II. Types of Battery Holder Materials
A. Plastic Materials
1. **ABS (Acrylonitrile Butadiene Styrene)**: ABS is a popular thermoplastic known for its strength and impact resistance. It is lightweight and can be easily molded into complex shapes, making it ideal for battery holders.
2. **Polycarbonate**: This material is known for its high impact resistance and transparency. Polycarbonate battery holders can withstand high temperatures and are often used in applications where durability is paramount.
3. **Nylon**: Nylon is a versatile plastic that offers excellent strength and flexibility. It is resistant to wear and tear, making it suitable for battery holders that require a snug fit.
B. Metal Materials
1. **Stainless Steel**: Known for its corrosion resistance and strength, stainless steel is often used in battery holders that require durability in harsh environments.
2. **Aluminum**: Lightweight and resistant to corrosion, aluminum is another popular choice for battery holders. Its excellent thermal conductivity also makes it suitable for applications where heat dissipation is necessary.
3. **Copper**: Copper is primarily used for its excellent electrical conductivity. Battery holders made from copper can provide efficient power transfer, although they may require additional coatings to prevent corrosion.
C. Composite Materials
1. **Hybrid Materials**: These materials combine the properties of plastics and metals to create a lightweight yet strong battery holder. They can be engineered to meet specific performance requirements.
2. **Advantages of Composites**: Composite materials often offer improved strength-to-weight ratios, enhanced thermal stability, and resistance to environmental factors, making them an attractive option for modern battery holders.
III. Common Production Processes for Battery Holder Materials
A. Injection Molding (for Plastic Materials)
1. **Process Description**: Injection molding involves injecting molten plastic into a mold to create the desired shape. This process is highly efficient for mass production.
2. **Advantages and Disadvantages**: The primary advantage of injection molding is its ability to produce complex shapes with high precision. However, the initial setup costs can be high, making it less economical for small production runs.
3. **Applications in Battery Holder Production**: Injection molding is widely used for producing plastic battery holders due to its efficiency and ability to create intricate designs.
B. Extrusion (for Plastic Materials)
1. **Process Description**: In extrusion, plastic is melted and forced through a die to create long shapes, which can then be cut to size. This process is ideal for producing continuous profiles.
2. **Advantages and Disadvantages**: Extrusion is cost-effective for large volumes but is limited to simpler shapes compared to injection molding.
3. **Applications in Battery Holder Production**: Extruded plastic components can be used in battery holders, particularly for creating channels or frames.
C. Stamping and Die-Cutting (for Metal Materials)
1. **Process Description**: Stamping involves pressing metal sheets into a die to create specific shapes. Die-cutting is similar but is often used for thinner materials.
2. **Advantages and Disadvantages**: Stamping is efficient for high-volume production and can produce precise shapes. However, it may not be suitable for complex designs.
3. **Applications in Battery Holder Production**: Stamping is commonly used for metal battery holders, especially those requiring flat components.
D. Machining (for Metal Materials)
1. **Process Description**: Machining involves removing material from a solid block to achieve the desired shape. This can be done through processes like milling, turning, or drilling.
2. **Advantages and Disadvantages**: Machining allows for high precision and the ability to create complex shapes. However, it can be time-consuming and costly for large production runs.
3. **Applications in Battery Holder Production**: Machining is often used for custom or low-volume production of metal battery holders.
E. 3D Printing (for Both Plastic and Composite Materials)
1. **Process Description**: 3D printing, or additive manufacturing, builds objects layer by layer from digital models. This process allows for rapid prototyping and customization.
2. **Advantages and Disadvantages**: The primary advantage of 3D printing is its flexibility in design and the ability to create complex geometries. However, it may not be as cost-effective for large-scale production.
3. **Applications in Battery Holder Production**: 3D printing is increasingly used for prototyping battery holders and producing small batches of customized designs.
IV. Quality Control in Production Processes
A. Importance of Quality Control
Quality control is essential in the production of battery holders to ensure that they meet safety and performance standards. Defective battery holders can lead to device failures, safety hazards, and increased costs.
B. Common Quality Control Methods
1. **Material Testing**: This involves testing the raw materials for properties such as strength, conductivity, and thermal stability to ensure they meet specifications.
2. **Dimensional Inspection**: Accurate measurements are taken to ensure that the produced battery holders conform to design specifications.
3. **Functional Testing**: This involves testing the battery holders in real-world conditions to ensure they perform as expected, including checking for secure battery connections and electrical conductivity.
V. Environmental Considerations
A. Sustainability in Battery Holder Production
As environmental concerns grow, manufacturers are increasingly focusing on sustainable practices in battery holder production. This includes using recyclable materials and reducing waste during production.
B. Recycling of Materials
Recycling plastic and metal materials used in battery holders can significantly reduce environmental impact. Many manufacturers are now implementing recycling programs to reclaim materials from used products.
C. Innovations in Eco-Friendly Materials
Research into biodegradable plastics and other eco-friendly materials is ongoing, with the goal of creating battery holders that are both functional and environmentally friendly.
VI. Future Trends in Battery Holder Production
A. Advances in Materials Science
Ongoing research in materials science is leading to the development of new materials that offer improved performance characteristics for battery holders, such as enhanced conductivity and durability.
B. Automation and Industry 4.0
The integration of automation and smart technologies in manufacturing processes is expected to increase efficiency and reduce costs in battery holder production.
C. Customization and Rapid Prototyping
As consumer demand for customized products grows, manufacturers are increasingly adopting rapid prototyping techniques, such as 3D printing, to create tailored battery holders quickly.
VII. Conclusion
In summary, understanding the common production processes for battery holder materials is crucial for manufacturers aiming to optimize performance and reduce costs. From the selection of materials to the various production techniques, each aspect plays a vital role in the final product's quality and functionality. As technology advances and environmental considerations become more pressing, the future of battery holder production looks promising, with innovations in materials and processes paving the way for more efficient and sustainable solutions. By staying informed about these trends, manufacturers can better position themselves in a competitive market and meet the evolving needs of consumers.
Common Production Processes for Battery Holder Materials
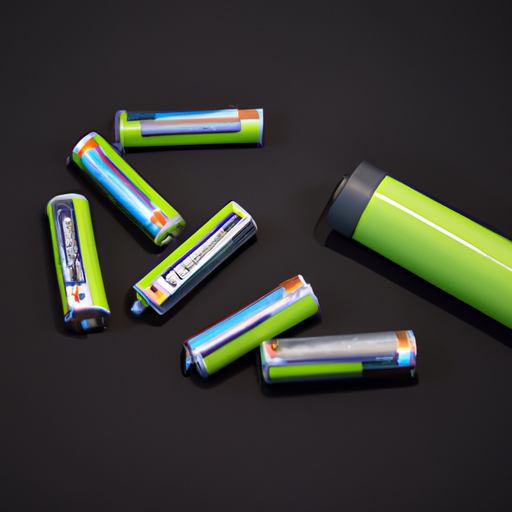
I. Introduction
Battery holders are essential components in a wide range of electronic devices, from remote controls to sophisticated medical equipment. They serve as the interface between the battery and the device, ensuring a secure connection that allows for efficient power transfer. The importance of battery holders cannot be overstated, as they play a critical role in the overall performance and reliability of electronic systems.
Battery holders are made from various materials, each chosen for its specific properties, such as durability, conductivity, and resistance to environmental factors. Understanding the common production processes for these materials is crucial for manufacturers aiming to optimize performance and reduce costs.
II. Types of Battery Holder Materials
A. Plastic Materials
1. **ABS (Acrylonitrile Butadiene Styrene)**: ABS is a popular thermoplastic known for its strength and impact resistance. It is lightweight and can be easily molded into complex shapes, making it ideal for battery holders.
2. **Polycarbonate**: This material is known for its high impact resistance and transparency. Polycarbonate battery holders can withstand high temperatures and are often used in applications where durability is paramount.
3. **Nylon**: Nylon is a versatile plastic that offers excellent strength and flexibility. It is resistant to wear and tear, making it suitable for battery holders that require a snug fit.
B. Metal Materials
1. **Stainless Steel**: Known for its corrosion resistance and strength, stainless steel is often used in battery holders that require durability in harsh environments.
2. **Aluminum**: Lightweight and resistant to corrosion, aluminum is another popular choice for battery holders. Its excellent thermal conductivity also makes it suitable for applications where heat dissipation is necessary.
3. **Copper**: Copper is primarily used for its excellent electrical conductivity. Battery holders made from copper can provide efficient power transfer, although they may require additional coatings to prevent corrosion.
C. Composite Materials
1. **Hybrid Materials**: These materials combine the properties of plastics and metals to create a lightweight yet strong battery holder. They can be engineered to meet specific performance requirements.
2. **Advantages of Composites**: Composite materials often offer improved strength-to-weight ratios, enhanced thermal stability, and resistance to environmental factors, making them an attractive option for modern battery holders.
III. Common Production Processes for Battery Holder Materials
A. Injection Molding (for Plastic Materials)
1. **Process Description**: Injection molding involves injecting molten plastic into a mold to create the desired shape. This process is highly efficient for mass production.
2. **Advantages and Disadvantages**: The primary advantage of injection molding is its ability to produce complex shapes with high precision. However, the initial setup costs can be high, making it less economical for small production runs.
3. **Applications in Battery Holder Production**: Injection molding is widely used for producing plastic battery holders due to its efficiency and ability to create intricate designs.
B. Extrusion (for Plastic Materials)
1. **Process Description**: In extrusion, plastic is melted and forced through a die to create long shapes, which can then be cut to size. This process is ideal for producing continuous profiles.
2. **Advantages and Disadvantages**: Extrusion is cost-effective for large volumes but is limited to simpler shapes compared to injection molding.
3. **Applications in Battery Holder Production**: Extruded plastic components can be used in battery holders, particularly for creating channels or frames.
C. Stamping and Die-Cutting (for Metal Materials)
1. **Process Description**: Stamping involves pressing metal sheets into a die to create specific shapes. Die-cutting is similar but is often used for thinner materials.
2. **Advantages and Disadvantages**: Stamping is efficient for high-volume production and can produce precise shapes. However, it may not be suitable for complex designs.
3. **Applications in Battery Holder Production**: Stamping is commonly used for metal battery holders, especially those requiring flat components.
D. Machining (for Metal Materials)
1. **Process Description**: Machining involves removing material from a solid block to achieve the desired shape. This can be done through processes like milling, turning, or drilling.
2. **Advantages and Disadvantages**: Machining allows for high precision and the ability to create complex shapes. However, it can be time-consuming and costly for large production runs.
3. **Applications in Battery Holder Production**: Machining is often used for custom or low-volume production of metal battery holders.
E. 3D Printing (for Both Plastic and Composite Materials)
1. **Process Description**: 3D printing, or additive manufacturing, builds objects layer by layer from digital models. This process allows for rapid prototyping and customization.
2. **Advantages and Disadvantages**: The primary advantage of 3D printing is its flexibility in design and the ability to create complex geometries. However, it may not be as cost-effective for large-scale production.
3. **Applications in Battery Holder Production**: 3D printing is increasingly used for prototyping battery holders and producing small batches of customized designs.
IV. Quality Control in Production Processes
A. Importance of Quality Control
Quality control is essential in the production of battery holders to ensure that they meet safety and performance standards. Defective battery holders can lead to device failures, safety hazards, and increased costs.
B. Common Quality Control Methods
1. **Material Testing**: This involves testing the raw materials for properties such as strength, conductivity, and thermal stability to ensure they meet specifications.
2. **Dimensional Inspection**: Accurate measurements are taken to ensure that the produced battery holders conform to design specifications.
3. **Functional Testing**: This involves testing the battery holders in real-world conditions to ensure they perform as expected, including checking for secure battery connections and electrical conductivity.
V. Environmental Considerations
A. Sustainability in Battery Holder Production
As environmental concerns grow, manufacturers are increasingly focusing on sustainable practices in battery holder production. This includes using recyclable materials and reducing waste during production.
B. Recycling of Materials
Recycling plastic and metal materials used in battery holders can significantly reduce environmental impact. Many manufacturers are now implementing recycling programs to reclaim materials from used products.
C. Innovations in Eco-Friendly Materials
Research into biodegradable plastics and other eco-friendly materials is ongoing, with the goal of creating battery holders that are both functional and environmentally friendly.
VI. Future Trends in Battery Holder Production
A. Advances in Materials Science
Ongoing research in materials science is leading to the development of new materials that offer improved performance characteristics for battery holders, such as enhanced conductivity and durability.
B. Automation and Industry 4.0
The integration of automation and smart technologies in manufacturing processes is expected to increase efficiency and reduce costs in battery holder production.
C. Customization and Rapid Prototyping
As consumer demand for customized products grows, manufacturers are increasingly adopting rapid prototyping techniques, such as 3D printing, to create tailored battery holders quickly.
VII. Conclusion
In summary, understanding the common production processes for battery holder materials is crucial for manufacturers aiming to optimize performance and reduce costs. From the selection of materials to the various production techniques, each aspect plays a vital role in the final product's quality and functionality. As technology advances and environmental considerations become more pressing, the future of battery holder production looks promising, with innovations in materials and processes paving the way for more efficient and sustainable solutions. By staying informed about these trends, manufacturers can better position themselves in a competitive market and meet the evolving needs of consumers.