Latest Manufacturing Processes for Battery Holders
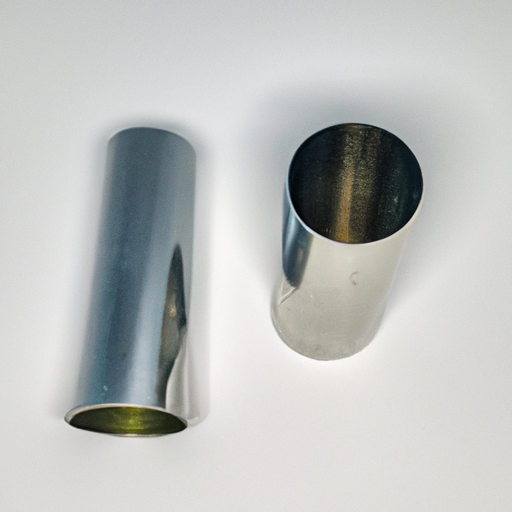
I. Introduction
Battery holders are essential components in a wide range of electronic devices, from remote controls to electric vehicles. They provide a secure and reliable way to house batteries, ensuring that they maintain a stable connection and are protected from environmental factors. As technology advances, the manufacturing processes for battery holders have evolved significantly, incorporating new materials and techniques that enhance performance, reduce costs, and improve sustainability. This blog post will explore the latest manufacturing processes for battery holders, highlighting traditional methods, advanced techniques, innovative materials, and future trends.
II. Traditional Manufacturing Processes
A. Injection Molding
Injection molding is one of the most widely used manufacturing processes for producing battery holders. This method involves injecting molten plastic into a mold, where it cools and solidifies into the desired shape. Common materials used in injection molding include acrylonitrile butadiene styrene (ABS), polycarbonate, and polypropylene.
**Advantages and Limitations:**
The primary advantage of injection molding is its ability to produce complex shapes with high precision and repeatability. It is also highly efficient for large production runs, as the process can be automated. However, the initial cost of creating molds can be high, making it less economical for small batches.
B. Stamping and Die-Cutting
Stamping and die-cutting are traditional methods used to manufacture battery holders, particularly those made from metal. Stamping involves pressing a sheet of metal into a die to create the desired shape, while die-cutting uses a similar process for non-metal materials.
**Pros and Cons of Stamping:**
Stamping is known for its speed and efficiency, making it suitable for high-volume production. It also allows for the creation of intricate designs. However, the process can be limited by the thickness of the material and may require additional finishing processes to achieve the desired surface quality.
III. Advanced Manufacturing Techniques
A. 3D Printing (Additive Manufacturing)
3D printing, or additive manufacturing, has revolutionized the production of battery holders by allowing for rapid prototyping and customization. This technology builds objects layer by layer from digital models, using materials such as thermoplastics, resins, and even metals.
**Benefits of 3D Printing:**
One of the key advantages of 3D printing is its ability to create complex geometries that would be difficult or impossible to achieve with traditional methods. It also enables manufacturers to quickly iterate designs, reducing time-to-market for new products. Additionally, 3D printing can minimize waste, as it uses only the material needed for the final product.
B. CNC Machining
Computer Numerical Control (CNC) machining is another advanced manufacturing technique that offers high precision and efficiency. This process involves the use of computer-controlled machines to remove material from a solid block to create the desired shape.
**Precision and Efficiency Advantages:**
CNC machining is particularly well-suited for producing battery holders from metals and composites, offering tight tolerances and excellent surface finishes. It is also highly flexible, allowing for quick changes in design without the need for new molds or tooling.
C. Laser Cutting and Engraving
Laser cutting and engraving are increasingly used in the manufacturing of battery holders, particularly for creating intricate designs and patterns. This technology uses focused laser beams to cut or engrave materials with high precision.
**Benefits of Precision and Design Flexibility:**
Laser cutting allows for clean edges and complex shapes, making it ideal for custom battery holders. It also reduces the need for secondary finishing processes, streamlining production. The ability to easily modify designs in software before cutting further enhances flexibility.
IV. Innovative Materials in Battery Holder Manufacturing
A. Thermoplastics and Composites
Thermoplastics, such as ABS and polycarbonate, are commonly used in battery holder manufacturing due to their lightweight and durable properties. Composites, which combine different materials to enhance performance, are also gaining popularity.
**Advantages of Composite Materials:**
Composite materials can offer improved strength-to-weight ratios and resistance to environmental factors, making them ideal for battery holders used in demanding applications.
B. Metal Alloys
Metal alloys, such as aluminum and stainless steel, are often used for battery holders that require enhanced durability and conductivity. These materials are particularly important in applications where heat dissipation and structural integrity are critical.
**Benefits of Using Metals:**
Metals provide excellent mechanical properties and can withstand harsh conditions, making them suitable for high-performance battery applications.
C. Sustainable Materials
As sustainability becomes a priority in manufacturing, eco-friendly materials are being explored for battery holder production. Biodegradable plastics and recycled materials are gaining traction as manufacturers seek to reduce their environmental impact.
**Impact of Sustainability on Manufacturing Processes:**
The use of sustainable materials can influence manufacturing processes, requiring adaptations in techniques and equipment to accommodate new material properties.
V. Automation and Industry 4.0
A. Role of Automation in Manufacturing
Automation plays a crucial role in modern battery holder manufacturing, enhancing efficiency and consistency. Automated processes can include everything from material handling to assembly and quality control.
**Benefits of Automation:**
Automation reduces labor costs, minimizes human error, and increases production speed. It also allows for real-time monitoring of processes, ensuring that quality standards are met consistently.
B. Integration of IoT and Smart Manufacturing
The Internet of Things (IoT) is transforming manufacturing by enabling machines and systems to communicate and share data. This integration allows for smarter manufacturing processes, where data analytics can optimize production and maintenance schedules.
**Benefits of Data Analytics and Real-Time Monitoring:**
IoT-enabled systems can provide insights into production efficiency, equipment performance, and potential issues before they become critical, leading to improved decision-making and reduced downtime.
VI. Quality Control and Testing
A. Importance of Quality Control in Battery Holder Manufacturing
Quality control is essential in battery holder manufacturing to ensure that products meet safety and performance standards. Rigorous testing and inspection processes are necessary to identify defects and ensure reliability.
B. Common Testing Methods
1. **Mechanical Testing:**
Mechanical tests assess the strength and durability of battery holders, ensuring they can withstand physical stresses.
2. **Electrical Testing:**
Electrical tests verify the conductivity and performance of battery holders, ensuring they provide a reliable connection for batteries.
3. **Environmental Testing:**
Environmental tests evaluate how battery holders perform under various conditions, such as temperature fluctuations and humidity.
C. Standards and Certifications
Manufacturers must adhere to industry standards and certifications to ensure their products are safe and reliable. Compliance with standards such as ISO and UL can enhance credibility and marketability.
VII. Future Trends in Battery Holder Manufacturing
A. Emerging Technologies
The future of battery holder manufacturing is likely to be shaped by emerging technologies, such as nanotechnology and smart materials. These advancements could lead to lighter, more efficient, and more durable battery holders.
B. Market Trends and Consumer Demands
As the demand for renewable energy sources and portable electronic devices continues to grow, manufacturers will need to adapt to changing consumer preferences. This shift may drive innovation in battery holder design and materials, focusing on efficiency and sustainability.
VIII. Conclusion
The manufacturing processes for battery holders have evolved significantly, driven by advancements in technology and materials. From traditional methods like injection molding and stamping to advanced techniques such as 3D printing and CNC machining, manufacturers are continually seeking ways to improve efficiency, precision, and sustainability. As the industry moves forward, embracing automation and innovative materials will be crucial in meeting the demands of a rapidly changing market. The future of battery holder manufacturing looks promising, with exciting developments on the horizon that will enhance performance and reduce environmental impact.
IX. References
A comprehensive list of academic papers, articles, and industry reports would typically follow here, providing sources for further reading and research on the topic.
Latest Manufacturing Processes for Battery Holders
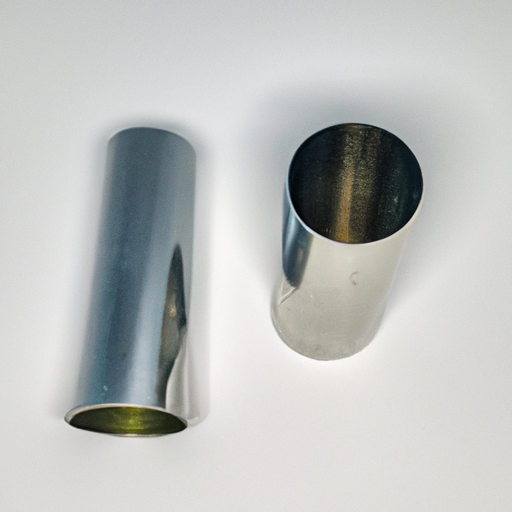
I. Introduction
Battery holders are essential components in a wide range of electronic devices, from remote controls to electric vehicles. They provide a secure and reliable way to house batteries, ensuring that they maintain a stable connection and are protected from environmental factors. As technology advances, the manufacturing processes for battery holders have evolved significantly, incorporating new materials and techniques that enhance performance, reduce costs, and improve sustainability. This blog post will explore the latest manufacturing processes for battery holders, highlighting traditional methods, advanced techniques, innovative materials, and future trends.
II. Traditional Manufacturing Processes
A. Injection Molding
Injection molding is one of the most widely used manufacturing processes for producing battery holders. This method involves injecting molten plastic into a mold, where it cools and solidifies into the desired shape. Common materials used in injection molding include acrylonitrile butadiene styrene (ABS), polycarbonate, and polypropylene.
**Advantages and Limitations:**
The primary advantage of injection molding is its ability to produce complex shapes with high precision and repeatability. It is also highly efficient for large production runs, as the process can be automated. However, the initial cost of creating molds can be high, making it less economical for small batches.
B. Stamping and Die-Cutting
Stamping and die-cutting are traditional methods used to manufacture battery holders, particularly those made from metal. Stamping involves pressing a sheet of metal into a die to create the desired shape, while die-cutting uses a similar process for non-metal materials.
**Pros and Cons of Stamping:**
Stamping is known for its speed and efficiency, making it suitable for high-volume production. It also allows for the creation of intricate designs. However, the process can be limited by the thickness of the material and may require additional finishing processes to achieve the desired surface quality.
III. Advanced Manufacturing Techniques
A. 3D Printing (Additive Manufacturing)
3D printing, or additive manufacturing, has revolutionized the production of battery holders by allowing for rapid prototyping and customization. This technology builds objects layer by layer from digital models, using materials such as thermoplastics, resins, and even metals.
**Benefits of 3D Printing:**
One of the key advantages of 3D printing is its ability to create complex geometries that would be difficult or impossible to achieve with traditional methods. It also enables manufacturers to quickly iterate designs, reducing time-to-market for new products. Additionally, 3D printing can minimize waste, as it uses only the material needed for the final product.
B. CNC Machining
Computer Numerical Control (CNC) machining is another advanced manufacturing technique that offers high precision and efficiency. This process involves the use of computer-controlled machines to remove material from a solid block to create the desired shape.
**Precision and Efficiency Advantages:**
CNC machining is particularly well-suited for producing battery holders from metals and composites, offering tight tolerances and excellent surface finishes. It is also highly flexible, allowing for quick changes in design without the need for new molds or tooling.
C. Laser Cutting and Engraving
Laser cutting and engraving are increasingly used in the manufacturing of battery holders, particularly for creating intricate designs and patterns. This technology uses focused laser beams to cut or engrave materials with high precision.
**Benefits of Precision and Design Flexibility:**
Laser cutting allows for clean edges and complex shapes, making it ideal for custom battery holders. It also reduces the need for secondary finishing processes, streamlining production. The ability to easily modify designs in software before cutting further enhances flexibility.
IV. Innovative Materials in Battery Holder Manufacturing
A. Thermoplastics and Composites
Thermoplastics, such as ABS and polycarbonate, are commonly used in battery holder manufacturing due to their lightweight and durable properties. Composites, which combine different materials to enhance performance, are also gaining popularity.
**Advantages of Composite Materials:**
Composite materials can offer improved strength-to-weight ratios and resistance to environmental factors, making them ideal for battery holders used in demanding applications.
B. Metal Alloys
Metal alloys, such as aluminum and stainless steel, are often used for battery holders that require enhanced durability and conductivity. These materials are particularly important in applications where heat dissipation and structural integrity are critical.
**Benefits of Using Metals:**
Metals provide excellent mechanical properties and can withstand harsh conditions, making them suitable for high-performance battery applications.
C. Sustainable Materials
As sustainability becomes a priority in manufacturing, eco-friendly materials are being explored for battery holder production. Biodegradable plastics and recycled materials are gaining traction as manufacturers seek to reduce their environmental impact.
**Impact of Sustainability on Manufacturing Processes:**
The use of sustainable materials can influence manufacturing processes, requiring adaptations in techniques and equipment to accommodate new material properties.
V. Automation and Industry 4.0
A. Role of Automation in Manufacturing
Automation plays a crucial role in modern battery holder manufacturing, enhancing efficiency and consistency. Automated processes can include everything from material handling to assembly and quality control.
**Benefits of Automation:**
Automation reduces labor costs, minimizes human error, and increases production speed. It also allows for real-time monitoring of processes, ensuring that quality standards are met consistently.
B. Integration of IoT and Smart Manufacturing
The Internet of Things (IoT) is transforming manufacturing by enabling machines and systems to communicate and share data. This integration allows for smarter manufacturing processes, where data analytics can optimize production and maintenance schedules.
**Benefits of Data Analytics and Real-Time Monitoring:**
IoT-enabled systems can provide insights into production efficiency, equipment performance, and potential issues before they become critical, leading to improved decision-making and reduced downtime.
VI. Quality Control and Testing
A. Importance of Quality Control in Battery Holder Manufacturing
Quality control is essential in battery holder manufacturing to ensure that products meet safety and performance standards. Rigorous testing and inspection processes are necessary to identify defects and ensure reliability.
B. Common Testing Methods
1. **Mechanical Testing:**
Mechanical tests assess the strength and durability of battery holders, ensuring they can withstand physical stresses.
2. **Electrical Testing:**
Electrical tests verify the conductivity and performance of battery holders, ensuring they provide a reliable connection for batteries.
3. **Environmental Testing:**
Environmental tests evaluate how battery holders perform under various conditions, such as temperature fluctuations and humidity.
C. Standards and Certifications
Manufacturers must adhere to industry standards and certifications to ensure their products are safe and reliable. Compliance with standards such as ISO and UL can enhance credibility and marketability.
VII. Future Trends in Battery Holder Manufacturing
A. Emerging Technologies
The future of battery holder manufacturing is likely to be shaped by emerging technologies, such as nanotechnology and smart materials. These advancements could lead to lighter, more efficient, and more durable battery holders.
B. Market Trends and Consumer Demands
As the demand for renewable energy sources and portable electronic devices continues to grow, manufacturers will need to adapt to changing consumer preferences. This shift may drive innovation in battery holder design and materials, focusing on efficiency and sustainability.
VIII. Conclusion
The manufacturing processes for battery holders have evolved significantly, driven by advancements in technology and materials. From traditional methods like injection molding and stamping to advanced techniques such as 3D printing and CNC machining, manufacturers are continually seeking ways to improve efficiency, precision, and sustainability. As the industry moves forward, embracing automation and innovative materials will be crucial in meeting the demands of a rapidly changing market. The future of battery holder manufacturing looks promising, with exciting developments on the horizon that will enhance performance and reduce environmental impact.
IX. References
A comprehensive list of academic papers, articles, and industry reports would typically follow here, providing sources for further reading and research on the topic.