What are the Popular Models of Mainstream 10 Top 4S Battery Holder Welding Tutorials?
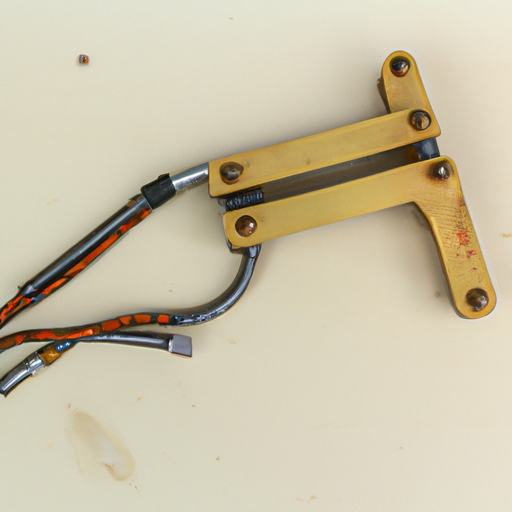
Introduction
In the world of electronics, battery holders play a crucial role in ensuring that power sources are securely and efficiently connected to devices. Among various configurations, the 4S battery setup—comprising four cells connected in series—has gained popularity, particularly in applications like drones, remote-controlled (RC) vehicles, and solar energy systems. This article aims to explore the popular models of 4S battery holders and provide detailed welding tutorials to help enthusiasts and professionals alike create reliable battery connections.
Section 1: Understanding 4S Battery Configurations
A 4S battery configuration consists of four individual battery cells connected in series, which increases the overall voltage while maintaining the same capacity as a single cell. For instance, using four 3.7V lithium-ion cells in series results in a total voltage of 14.8V. This configuration is widely used in applications that require higher voltage outputs, such as drones and RC vehicles, where performance and efficiency are paramount.
Proper battery holder design is essential for safety and efficiency. A well-designed holder not only secures the batteries but also ensures that connections are stable and can handle the required current without overheating or failing.
Section 2: Popular Models of 4S Battery Holders
2.1 Model 1: Standard Plastic Holders
Standard plastic holders are the most common type of battery holder. They are lightweight, affordable, and easy to use. These holders typically feature spring-loaded contacts that securely hold the batteries in place.
**Pros:**
- Cost-effective
- Lightweight
- Easy to assemble
**Cons:**
- Limited durability
- May not withstand high temperatures
**Recommended Applications:**
- General-purpose electronics projects
2.2 Model 2: Metal Holders
Metal holders offer enhanced durability and heat resistance compared to plastic options. They are often used in high-performance applications where reliability is critical.
**Pros:**
- Durable and long-lasting
- Better heat dissipation
**Cons:**
- Heavier than plastic holders
- More expensive
**Recommended Applications:**
- High-performance RC vehicles and drones
2.3 Model 3: Custom 3D-Printed Holders
With the rise of 3D printing technology, custom battery holders can be designed and printed to meet specific project requirements. This allows for unique shapes and sizes tailored to individual needs.
**Pros:**
- Fully customizable
- Can be designed for specific applications
**Cons:**
- Requires access to a 3D printer
- May not be as durable as metal holders
**Recommended Applications:**
- Unique or specialized projects
2.4 Model 4: Integrated Battery Management Systems (BMS)
Some battery holders come with integrated Battery Management Systems (BMS) that monitor and manage the charging and discharging of the batteries. This feature enhances safety and prolongs battery life.
**Pros:**
- Enhanced safety features
- Prolongs battery lifespan
**Cons:**
- More complex and expensive
- Requires additional knowledge to use effectively
**Recommended Applications:**
- Advanced projects requiring battery management
2.5 Model 5: Modular Holders
Modular holders allow users to connect multiple battery packs together, making them versatile for various applications. They can be easily expanded or modified as needed.
**Pros:**
- Versatile and expandable
- Easy to modify
**Cons:**
- May require additional connectors
- Can be bulkier
**Recommended Applications:**
- Projects that require scalability
2.6 Model 6: High-Temperature Resistant Holders
These holders are designed to withstand high temperatures, making them suitable for applications where heat is a concern, such as in high-performance motors.
**Pros:**
- Heat-resistant
- Durable
**Cons:**
- Typically more expensive
- Limited availability
**Recommended Applications:**
- High-performance applications
2.7 Model 7: Waterproof Holders
Waterproof holders are essential for projects exposed to moisture or harsh environments. They protect the batteries from water damage, ensuring reliable performance.
**Pros:**
- Protects against moisture
- Enhances durability
**Cons:**
- Heavier and bulkier
- More expensive
**Recommended Applications:**
- Outdoor projects and marine applications
2.8 Model 8: Lightweight Holders
For applications where weight is a critical factor, lightweight holders made from materials like carbon fiber or lightweight plastics are ideal.
**Pros:**
- Reduces overall weight
- Easy to handle
**Cons:**
- May sacrifice durability
- Can be more expensive
**Recommended Applications:**
- Drones and racing vehicles
2.9 Model 9: Holders with Built-in Connectors
These holders come with built-in connectors, simplifying the process of connecting batteries to devices. They save time and reduce the need for additional wiring.
**Pros:**
- Simplifies connections
- Reduces assembly time
**Cons:**
- Limited customization options
- May be more expensive
**Recommended Applications:**
- Quick assembly projects
2.10 Model 10: Holders with Safety Features
Some holders are designed with additional safety features, such as fuses or thermal cutoffs, to prevent overheating and short circuits.
**Pros:**
- Enhanced safety
- Reduces risk of battery failure
**Cons:**
- More complex design
- Higher cost
**Recommended Applications:**
- Projects where safety is a top priority
Section 3: Welding Techniques for 4S Battery Holders
3.1 Safety Precautions
Before starting any welding project, it is crucial to prioritize safety. Wear appropriate safety gear, including goggles, gloves, and a mask. Ensure your workspace is well-ventilated and free from flammable materials.
3.2 Tools and Materials Needed
To successfully weld a 4S battery holder, you will need the following tools and materials:
- Soldering iron
- Solder (preferably rosin-core)
- Wire cutters and strippers
- Heat shrink tubing
- Battery holder
- Wires and connectors
3.3 Step-by-Step Welding Tutorial
Step 1: Preparing the Workspace
Set up a clean and organized workspace. Ensure that your tools are within reach and that you have adequate lighting.
Step 2: Preparing the Battery Holder
Inspect the battery holder for any defects. Clean the contact points with isopropyl alcohol to ensure a good connection.
Step 3: Cutting and Stripping Wires
Cut the wires to the desired length and strip about 1/4 inch of insulation from each end. Be careful not to damage the wire strands.
Step 4: Soldering the Connections
Heat the soldering iron and apply solder to the contact points on the battery holder. Quickly place the stripped wire onto the solder and allow it to melt and bond. Remove the soldering iron and let the connection cool.
**Tips:**
- Use a small amount of solder to avoid creating a blob.
- Ensure that the wire is securely attached and that there are no cold solder joints.
Step 5: Testing the Connections
After soldering, use a multimeter to test the connections for continuity. This step ensures that there are no shorts or open circuits.
Step 6: Final Assembly
Once all connections are tested and secure, assemble the battery holder. Use heat shrink tubing to cover exposed wires and connections for added protection.
Section 4: Troubleshooting Common Issues
During the welding process, you may encounter common issues such as cold solder joints, shorts, or weak connections. Here are some solutions:
Cold Solder Joints: Reheat the joint and add a small amount of solder to ensure a strong connection.
Short Circuits: Inspect the wiring for any exposed strands and insulate them with heat shrink tubing.
Weak Connections: Re-solder the connection, ensuring that the wire is securely attached.
Section 5: Conclusion
Choosing the right battery holder is essential for the success of your electronic projects. With various models available, each offering unique features and benefits, it’s important to consider your specific needs and applications. Experimenting with different holders and welding techniques can lead to improved performance and reliability in your projects. As technology continues to evolve, the future of battery holder design and DIY projects looks promising, offering even more opportunities for innovation and creativity.
References
For further reading and tutorials on battery holder welding techniques, consider exploring the following resources:
- Online forums and communities dedicated to electronics and DIY projects.
- YouTube channels that specialize in electronics tutorials.
- Manufacturer websites for specific battery holder models and specifications.
By understanding the various models of 4S battery holders and mastering the welding techniques, you can enhance your skills and create reliable power solutions for your electronic projects.
What are the Popular Models of Mainstream 10 Top 4S Battery Holder Welding Tutorials?
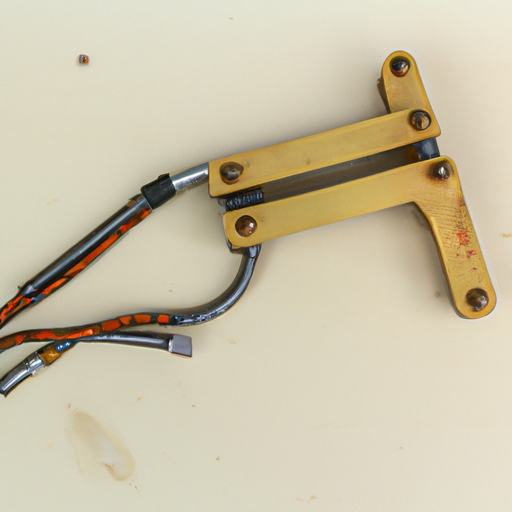
Introduction
In the world of electronics, battery holders play a crucial role in ensuring that power sources are securely and efficiently connected to devices. Among various configurations, the 4S battery setup—comprising four cells connected in series—has gained popularity, particularly in applications like drones, remote-controlled (RC) vehicles, and solar energy systems. This article aims to explore the popular models of 4S battery holders and provide detailed welding tutorials to help enthusiasts and professionals alike create reliable battery connections.
Section 1: Understanding 4S Battery Configurations
A 4S battery configuration consists of four individual battery cells connected in series, which increases the overall voltage while maintaining the same capacity as a single cell. For instance, using four 3.7V lithium-ion cells in series results in a total voltage of 14.8V. This configuration is widely used in applications that require higher voltage outputs, such as drones and RC vehicles, where performance and efficiency are paramount.
Proper battery holder design is essential for safety and efficiency. A well-designed holder not only secures the batteries but also ensures that connections are stable and can handle the required current without overheating or failing.
Section 2: Popular Models of 4S Battery Holders
2.1 Model 1: Standard Plastic Holders
Standard plastic holders are the most common type of battery holder. They are lightweight, affordable, and easy to use. These holders typically feature spring-loaded contacts that securely hold the batteries in place.
**Pros:**
- Cost-effective
- Lightweight
- Easy to assemble
**Cons:**
- Limited durability
- May not withstand high temperatures
**Recommended Applications:**
- General-purpose electronics projects
2.2 Model 2: Metal Holders
Metal holders offer enhanced durability and heat resistance compared to plastic options. They are often used in high-performance applications where reliability is critical.
**Pros:**
- Durable and long-lasting
- Better heat dissipation
**Cons:**
- Heavier than plastic holders
- More expensive
**Recommended Applications:**
- High-performance RC vehicles and drones
2.3 Model 3: Custom 3D-Printed Holders
With the rise of 3D printing technology, custom battery holders can be designed and printed to meet specific project requirements. This allows for unique shapes and sizes tailored to individual needs.
**Pros:**
- Fully customizable
- Can be designed for specific applications
**Cons:**
- Requires access to a 3D printer
- May not be as durable as metal holders
**Recommended Applications:**
- Unique or specialized projects
2.4 Model 4: Integrated Battery Management Systems (BMS)
Some battery holders come with integrated Battery Management Systems (BMS) that monitor and manage the charging and discharging of the batteries. This feature enhances safety and prolongs battery life.
**Pros:**
- Enhanced safety features
- Prolongs battery lifespan
**Cons:**
- More complex and expensive
- Requires additional knowledge to use effectively
**Recommended Applications:**
- Advanced projects requiring battery management
2.5 Model 5: Modular Holders
Modular holders allow users to connect multiple battery packs together, making them versatile for various applications. They can be easily expanded or modified as needed.
**Pros:**
- Versatile and expandable
- Easy to modify
**Cons:**
- May require additional connectors
- Can be bulkier
**Recommended Applications:**
- Projects that require scalability
2.6 Model 6: High-Temperature Resistant Holders
These holders are designed to withstand high temperatures, making them suitable for applications where heat is a concern, such as in high-performance motors.
**Pros:**
- Heat-resistant
- Durable
**Cons:**
- Typically more expensive
- Limited availability
**Recommended Applications:**
- High-performance applications
2.7 Model 7: Waterproof Holders
Waterproof holders are essential for projects exposed to moisture or harsh environments. They protect the batteries from water damage, ensuring reliable performance.
**Pros:**
- Protects against moisture
- Enhances durability
**Cons:**
- Heavier and bulkier
- More expensive
**Recommended Applications:**
- Outdoor projects and marine applications
2.8 Model 8: Lightweight Holders
For applications where weight is a critical factor, lightweight holders made from materials like carbon fiber or lightweight plastics are ideal.
**Pros:**
- Reduces overall weight
- Easy to handle
**Cons:**
- May sacrifice durability
- Can be more expensive
**Recommended Applications:**
- Drones and racing vehicles
2.9 Model 9: Holders with Built-in Connectors
These holders come with built-in connectors, simplifying the process of connecting batteries to devices. They save time and reduce the need for additional wiring.
**Pros:**
- Simplifies connections
- Reduces assembly time
**Cons:**
- Limited customization options
- May be more expensive
**Recommended Applications:**
- Quick assembly projects
2.10 Model 10: Holders with Safety Features
Some holders are designed with additional safety features, such as fuses or thermal cutoffs, to prevent overheating and short circuits.
**Pros:**
- Enhanced safety
- Reduces risk of battery failure
**Cons:**
- More complex design
- Higher cost
**Recommended Applications:**
- Projects where safety is a top priority
Section 3: Welding Techniques for 4S Battery Holders
3.1 Safety Precautions
Before starting any welding project, it is crucial to prioritize safety. Wear appropriate safety gear, including goggles, gloves, and a mask. Ensure your workspace is well-ventilated and free from flammable materials.
3.2 Tools and Materials Needed
To successfully weld a 4S battery holder, you will need the following tools and materials:
- Soldering iron
- Solder (preferably rosin-core)
- Wire cutters and strippers
- Heat shrink tubing
- Battery holder
- Wires and connectors
3.3 Step-by-Step Welding Tutorial
Step 1: Preparing the Workspace
Set up a clean and organized workspace. Ensure that your tools are within reach and that you have adequate lighting.
Step 2: Preparing the Battery Holder
Inspect the battery holder for any defects. Clean the contact points with isopropyl alcohol to ensure a good connection.
Step 3: Cutting and Stripping Wires
Cut the wires to the desired length and strip about 1/4 inch of insulation from each end. Be careful not to damage the wire strands.
Step 4: Soldering the Connections
Heat the soldering iron and apply solder to the contact points on the battery holder. Quickly place the stripped wire onto the solder and allow it to melt and bond. Remove the soldering iron and let the connection cool.
**Tips:**
- Use a small amount of solder to avoid creating a blob.
- Ensure that the wire is securely attached and that there are no cold solder joints.
Step 5: Testing the Connections
After soldering, use a multimeter to test the connections for continuity. This step ensures that there are no shorts or open circuits.
Step 6: Final Assembly
Once all connections are tested and secure, assemble the battery holder. Use heat shrink tubing to cover exposed wires and connections for added protection.
Section 4: Troubleshooting Common Issues
During the welding process, you may encounter common issues such as cold solder joints, shorts, or weak connections. Here are some solutions:
Cold Solder Joints: Reheat the joint and add a small amount of solder to ensure a strong connection.
Short Circuits: Inspect the wiring for any exposed strands and insulate them with heat shrink tubing.
Weak Connections: Re-solder the connection, ensuring that the wire is securely attached.
Section 5: Conclusion
Choosing the right battery holder is essential for the success of your electronic projects. With various models available, each offering unique features and benefits, it’s important to consider your specific needs and applications. Experimenting with different holders and welding techniques can lead to improved performance and reliability in your projects. As technology continues to evolve, the future of battery holder design and DIY projects looks promising, offering even more opportunities for innovation and creativity.
References
For further reading and tutorials on battery holder welding techniques, consider exploring the following resources:
- Online forums and communities dedicated to electronics and DIY projects.
- YouTube channels that specialize in electronics tutorials.
- Manufacturer websites for specific battery holder models and specifications.
By understanding the various models of 4S battery holders and mastering the welding techniques, you can enhance your skills and create reliable power solutions for your electronic projects.