Manufacturing Processes for the Latest Electronic Products Using Batteries
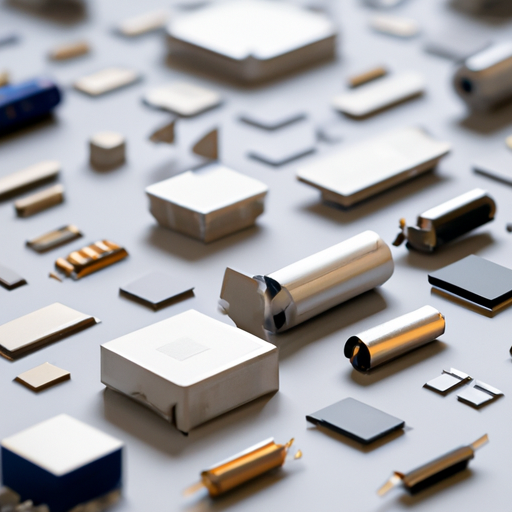
I. Introduction
In today's fast-paced technological landscape, batteries play a pivotal role in powering a wide array of electronic products, from smartphones and laptops to electric vehicles and smart home devices. The evolution of battery technology has been remarkable, transitioning from bulky, low-capacity options to sleek, high-performance solutions that are integral to modern life. This article aims to explore the manufacturing processes behind the latest electronic products that utilize batteries, shedding light on the intricate steps involved in bringing these innovations to market.
II. Types of Batteries Used in Electronic Products
A. Lithium-ion Batteries
Lithium-ion (Li-ion) batteries are the most prevalent type of battery used in consumer electronics today. Known for their high energy density, lightweight design, and ability to recharge quickly, Li-ion batteries are found in devices such as smartphones, laptops, and tablets. Their advantages include a longer lifespan compared to other battery types and minimal memory effect, which allows them to maintain capacity over time.
B. Nickel-Metal Hydride (NiMH) Batteries
NiMH batteries, while less common than Li-ion, are still widely used in specific applications, particularly in hybrid vehicles and rechargeable household devices. They offer a good balance between capacity and cost, making them a popular choice for products like digital cameras and cordless power tools. NiMH batteries are also more environmentally friendly than some alternatives, as they do not contain toxic heavy metals.
C. Solid-State Batteries
Emerging as a promising technology, solid-state batteries utilize a solid electrolyte instead of a liquid one, which enhances safety and energy density. Although still in the developmental stage, solid-state batteries have the potential to revolutionize the industry, particularly in electric vehicles and portable electronics, by providing longer ranges and faster charging times.
D. Other Battery Technologies
While Li-ion and NiMH dominate the market, other battery technologies, such as lead-acid and alkaline batteries, still find their place in specific applications. Lead-acid batteries are commonly used in automotive applications, while alkaline batteries are prevalent in household devices like remote controls and flashlights.
III. Overview of the Manufacturing Process
A. Design and Prototyping
The manufacturing process begins with the design and prototyping phase. Engineers conceptualize the product, considering factors such as functionality, aesthetics, and user experience. Computer-Aided Design (CAD) modeling and simulations are employed to create detailed blueprints, allowing for adjustments before moving to production.
B. Material Selection
Choosing the right materials is crucial for both the battery and the electronic device. Manufacturers must consider performance, cost, and environmental impact. Sustainable practices are increasingly prioritized, with a focus on sourcing materials responsibly and minimizing waste.
C. Battery Cell Manufacturing
The heart of battery production lies in the manufacturing of battery cells, which involves several key steps:
1. **Electrode Preparation**: This includes coating processes where active materials are applied to metal foils, followed by drying and calendaring to achieve the desired thickness and density.
2. **Cell Assembly**: Depending on the battery design, cells may be assembled using stacking or winding techniques. This is followed by electrolyte filling, which is critical for the battery's performance.
3. **Sealing and Packaging**: Once assembled, cells are sealed to prevent leakage and packaged for distribution. This step is vital for ensuring the longevity and safety of the battery.
D. Integration of Battery into Electronic Products
After the battery cells are manufactured, they are integrated into the electronic products. This involves:
1. **Circuit Design and PCB Manufacturing**: Engineers design the circuit boards that will house the battery and other electronic components, ensuring compatibility and efficiency.
2. **Assembly of Electronic Components**: The assembly line brings together various components, including the battery, display, and processors, to create the final product.
3. **Testing and Quality Assurance**: Rigorous testing is conducted to ensure that the product meets safety and performance standards before it reaches consumers.
IV. Advanced Manufacturing Techniques
A. Automation and Robotics
Automation and robotics have transformed battery manufacturing, enhancing efficiency and precision. Automated systems can handle repetitive tasks, reducing human error and increasing production speed. Robotics also play a crucial role in assembly lines, allowing for the seamless integration of components.
B. Additive Manufacturing (3D Printing)
Additive manufacturing, or 3D printing, is making waves in battery design and production. This technology allows for rapid prototyping and customization, enabling manufacturers to create complex geometries that were previously impossible. The advantages of 3D printing include reduced material waste and shorter lead times.
C. Nanotechnology in Battery Manufacturing
Nanotechnology is revolutionizing battery performance by enabling the development of materials at the molecular level. This can lead to batteries with higher capacities, faster charging times, and improved safety. As research in this field progresses, we can expect significant advancements in the capabilities of electronic products.
V. Quality Control and Testing
Quality control is paramount in battery manufacturing, as defects can lead to safety hazards and product failures. Manufacturers employ various testing methods to ensure battery performance, including:
1. **Capacity Testing**: Evaluating the battery's ability to hold charge over time.
2. **Cycle Life Testing**: Assessing how many charge-discharge cycles a battery can undergo before its performance degrades.
3. **Safety Testing**: Conducting rigorous tests to ensure that batteries can withstand extreme conditions without failing.
Regulatory compliance and certifications are also critical, as they ensure that products meet industry standards and safety regulations.
VI. Environmental Considerations
As the demand for batteries grows, so do concerns about their environmental impact. Sustainable manufacturing practices are becoming increasingly important, with a focus on reducing carbon footprints and minimizing waste. Additionally, recycling and proper disposal of batteries are essential to prevent environmental contamination and recover valuable materials.
VII. Future Trends in Battery Manufacturing
The future of battery manufacturing is bright, with ongoing innovations poised to reshape the industry. Advancements in battery technology, such as improved energy densities and faster charging capabilities, are on the horizon. Research and development will play a crucial role in driving these innovations, ensuring that electronic products continue to evolve and meet consumer demands.
VIII. Conclusion
The manufacturing processes behind the latest electronic products utilizing batteries are complex and multifaceted. From the initial design phase to the final assembly and testing, each step is critical to ensuring the safety and performance of these devices. As battery technology continues to evolve, so too will the manufacturing processes that support it, paving the way for a future filled with innovative electronic products that enhance our daily lives.
IX. References
A comprehensive list of academic papers, articles, and resources for further reading would typically follow here, providing readers with additional insights into the topics discussed in this article.
---
This blog post provides a detailed overview of the manufacturing processes for electronic products that utilize batteries, highlighting the significance of each step and the advancements shaping the future of the industry.
Manufacturing Processes for the Latest Electronic Products Using Batteries
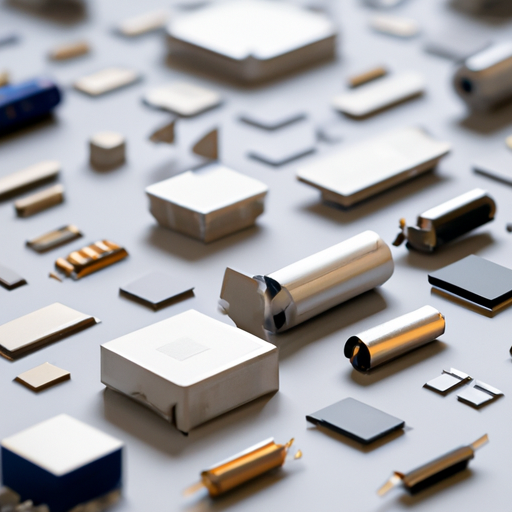
I. Introduction
In today's fast-paced technological landscape, batteries play a pivotal role in powering a wide array of electronic products, from smartphones and laptops to electric vehicles and smart home devices. The evolution of battery technology has been remarkable, transitioning from bulky, low-capacity options to sleek, high-performance solutions that are integral to modern life. This article aims to explore the manufacturing processes behind the latest electronic products that utilize batteries, shedding light on the intricate steps involved in bringing these innovations to market.
II. Types of Batteries Used in Electronic Products
A. Lithium-ion Batteries
Lithium-ion (Li-ion) batteries are the most prevalent type of battery used in consumer electronics today. Known for their high energy density, lightweight design, and ability to recharge quickly, Li-ion batteries are found in devices such as smartphones, laptops, and tablets. Their advantages include a longer lifespan compared to other battery types and minimal memory effect, which allows them to maintain capacity over time.
B. Nickel-Metal Hydride (NiMH) Batteries
NiMH batteries, while less common than Li-ion, are still widely used in specific applications, particularly in hybrid vehicles and rechargeable household devices. They offer a good balance between capacity and cost, making them a popular choice for products like digital cameras and cordless power tools. NiMH batteries are also more environmentally friendly than some alternatives, as they do not contain toxic heavy metals.
C. Solid-State Batteries
Emerging as a promising technology, solid-state batteries utilize a solid electrolyte instead of a liquid one, which enhances safety and energy density. Although still in the developmental stage, solid-state batteries have the potential to revolutionize the industry, particularly in electric vehicles and portable electronics, by providing longer ranges and faster charging times.
D. Other Battery Technologies
While Li-ion and NiMH dominate the market, other battery technologies, such as lead-acid and alkaline batteries, still find their place in specific applications. Lead-acid batteries are commonly used in automotive applications, while alkaline batteries are prevalent in household devices like remote controls and flashlights.
III. Overview of the Manufacturing Process
A. Design and Prototyping
The manufacturing process begins with the design and prototyping phase. Engineers conceptualize the product, considering factors such as functionality, aesthetics, and user experience. Computer-Aided Design (CAD) modeling and simulations are employed to create detailed blueprints, allowing for adjustments before moving to production.
B. Material Selection
Choosing the right materials is crucial for both the battery and the electronic device. Manufacturers must consider performance, cost, and environmental impact. Sustainable practices are increasingly prioritized, with a focus on sourcing materials responsibly and minimizing waste.
C. Battery Cell Manufacturing
The heart of battery production lies in the manufacturing of battery cells, which involves several key steps:
1. **Electrode Preparation**: This includes coating processes where active materials are applied to metal foils, followed by drying and calendaring to achieve the desired thickness and density.
2. **Cell Assembly**: Depending on the battery design, cells may be assembled using stacking or winding techniques. This is followed by electrolyte filling, which is critical for the battery's performance.
3. **Sealing and Packaging**: Once assembled, cells are sealed to prevent leakage and packaged for distribution. This step is vital for ensuring the longevity and safety of the battery.
D. Integration of Battery into Electronic Products
After the battery cells are manufactured, they are integrated into the electronic products. This involves:
1. **Circuit Design and PCB Manufacturing**: Engineers design the circuit boards that will house the battery and other electronic components, ensuring compatibility and efficiency.
2. **Assembly of Electronic Components**: The assembly line brings together various components, including the battery, display, and processors, to create the final product.
3. **Testing and Quality Assurance**: Rigorous testing is conducted to ensure that the product meets safety and performance standards before it reaches consumers.
IV. Advanced Manufacturing Techniques
A. Automation and Robotics
Automation and robotics have transformed battery manufacturing, enhancing efficiency and precision. Automated systems can handle repetitive tasks, reducing human error and increasing production speed. Robotics also play a crucial role in assembly lines, allowing for the seamless integration of components.
B. Additive Manufacturing (3D Printing)
Additive manufacturing, or 3D printing, is making waves in battery design and production. This technology allows for rapid prototyping and customization, enabling manufacturers to create complex geometries that were previously impossible. The advantages of 3D printing include reduced material waste and shorter lead times.
C. Nanotechnology in Battery Manufacturing
Nanotechnology is revolutionizing battery performance by enabling the development of materials at the molecular level. This can lead to batteries with higher capacities, faster charging times, and improved safety. As research in this field progresses, we can expect significant advancements in the capabilities of electronic products.
V. Quality Control and Testing
Quality control is paramount in battery manufacturing, as defects can lead to safety hazards and product failures. Manufacturers employ various testing methods to ensure battery performance, including:
1. **Capacity Testing**: Evaluating the battery's ability to hold charge over time.
2. **Cycle Life Testing**: Assessing how many charge-discharge cycles a battery can undergo before its performance degrades.
3. **Safety Testing**: Conducting rigorous tests to ensure that batteries can withstand extreme conditions without failing.
Regulatory compliance and certifications are also critical, as they ensure that products meet industry standards and safety regulations.
VI. Environmental Considerations
As the demand for batteries grows, so do concerns about their environmental impact. Sustainable manufacturing practices are becoming increasingly important, with a focus on reducing carbon footprints and minimizing waste. Additionally, recycling and proper disposal of batteries are essential to prevent environmental contamination and recover valuable materials.
VII. Future Trends in Battery Manufacturing
The future of battery manufacturing is bright, with ongoing innovations poised to reshape the industry. Advancements in battery technology, such as improved energy densities and faster charging capabilities, are on the horizon. Research and development will play a crucial role in driving these innovations, ensuring that electronic products continue to evolve and meet consumer demands.
VIII. Conclusion
The manufacturing processes behind the latest electronic products utilizing batteries are complex and multifaceted. From the initial design phase to the final assembly and testing, each step is critical to ensuring the safety and performance of these devices. As battery technology continues to evolve, so too will the manufacturing processes that support it, paving the way for a future filled with innovative electronic products that enhance our daily lives.
IX. References
A comprehensive list of academic papers, articles, and resources for further reading would typically follow here, providing readers with additional insights into the topics discussed in this article.
---
This blog post provides a detailed overview of the manufacturing processes for electronic products that utilize batteries, highlighting the significance of each step and the advancements shaping the future of the industry.