Common Production Process of Lithium Batteries
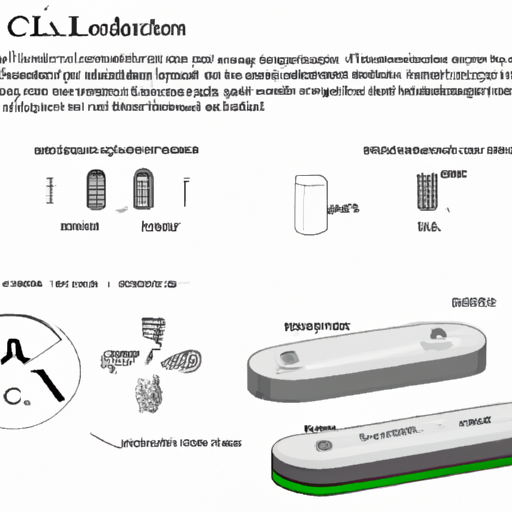
I. Introduction
Lithium batteries have become a cornerstone of modern technology, powering everything from smartphones and laptops to electric vehicles and renewable energy storage systems. Their lightweight, high energy density, and long cycle life make them the preferred choice for a wide range of applications across various industries. As the demand for energy storage solutions continues to rise, understanding the production process of lithium batteries is crucial for consumers, manufacturers, and policymakers alike. This article aims to educate readers on the common production process of lithium batteries, highlighting the significance of each step involved.
II. Understanding Lithium Batteries
A. Definition and Types of Lithium Batteries
Lithium batteries are rechargeable energy storage devices that utilize lithium ions to transfer energy between the anode and cathode during charging and discharging cycles. The two most common types of lithium batteries are:
1. **Lithium-ion (Li-ion) Batteries**: These batteries are widely used in consumer electronics and electric vehicles due to their high energy density and efficiency. They typically consist of a lithium cobalt oxide cathode and a graphite anode.
2. **Lithium Polymer (LiPo) Batteries**: LiPo batteries are known for their flexibility in shape and size, making them ideal for applications where space is limited, such as drones and wearable devices. They use a polymer electrolyte instead of a liquid electrolyte, allowing for a lighter and more compact design.
B. Key Components of Lithium Batteries
The main components of lithium batteries include:
1. **Anode**: The negative electrode, usually made of graphite, where lithium ions are stored during charging.
2. **Cathode**: The positive electrode, typically composed of lithium metal oxides, where lithium ions are released during discharge.
3. **Electrolyte**: A medium that allows the movement of lithium ions between the anode and cathode. It can be a liquid, gel, or solid.
4. **Separator**: A porous membrane that prevents direct contact between the anode and cathode while allowing lithium ions to pass through.
III. Raw Material Sourcing
A. Overview of Raw Materials
The production of lithium batteries begins with sourcing raw materials. Key materials include:
1. **Lithium Sources**: Lithium can be extracted from hard rock deposits (spodumene) or from brine sources found in salt flats. Each source has its own extraction and processing methods.
2. **Other Materials**: In addition to lithium, other essential materials include cobalt, nickel, and graphite. These materials contribute to the battery's performance and longevity.
B. Environmental and Ethical Considerations
The extraction of raw materials for lithium batteries raises environmental and ethical concerns. Mining practices can lead to habitat destruction, water depletion, and pollution. Additionally, the supply chain for materials like cobalt often involves labor practices that raise human rights concerns. As such, there is a growing emphasis on sourcing materials responsibly and ensuring supply chain transparency.
IV. Battery Cell Manufacturing Process
A. Electrode Preparation
The manufacturing process of lithium batteries involves several key steps:
1. **Mixing Active Materials**: The active materials for the anode and cathode are mixed with binders and solvents to create a slurry.
2. **Coating Processes**: The slurry is then coated onto metal foils (copper for the anode and aluminum for the cathode) to form thin films.
3. **Drying and Calendaring**: The coated films are dried to remove solvents and then compressed to achieve the desired thickness and density.
B. Cell Assembly
Once the electrodes are prepared, the next step is cell assembly:
1. **Stacking or Winding Electrodes**: The anode and cathode are either stacked or wound together with separators in between.
2. **Inserting Separators**: The separator is inserted to prevent short circuits while allowing lithium ions to pass through.
3. **Filling with Electrolyte**: The assembled cell is filled with electrolyte, which facilitates ion movement during charging and discharging.
C. Sealing and Packaging
The final step in cell manufacturing involves sealing and packaging:
1. **Cell Casing Options**: The cells are encased in protective materials, which can vary from cylindrical to prismatic shapes.
2. **Ensuring Safety and Integrity**: The sealing process is critical to prevent leakage and ensure the safety of the battery during operation.
V. Formation and Testing
A. Initial Formation Process
After assembly, the batteries undergo an initial formation process:
1. **Charging and Discharging Cycles**: The cells are subjected to several charging and discharging cycles to establish their performance characteristics.
2. **Establishing Battery Performance**: This process helps in determining the battery's capacity, voltage, and overall efficiency.
B. Quality Control Measures
Quality control is essential in battery production:
1. **Testing for Capacity, Voltage, and Safety**: Each battery is tested to ensure it meets the required specifications and safety standards.
2. **Identifying Defects and Ensuring Reliability**: Any defects are identified and addressed to ensure the reliability and longevity of the batteries.
VI. Battery Management Systems (BMS)
A. Role of BMS in Lithium Batteries
Battery Management Systems (BMS) play a crucial role in the operation of lithium batteries:
1. **Monitoring Battery Health**: BMS continuously monitors the state of charge, temperature, and overall health of the battery.
2. **Ensuring Safety During Operation**: The system prevents overcharging, overheating, and other conditions that could lead to battery failure or safety hazards.
B. Integration with Battery Production
The design and integration of BMS are essential for optimal battery performance:
1. **Designing BMS for Specific Applications**: BMS can be tailored to meet the specific needs of different applications, such as electric vehicles or renewable energy systems.
2. **Testing and Validation**: Rigorous testing ensures that the BMS functions correctly and enhances the safety and efficiency of the battery.
VII. Environmental Impact and Recycling
A. Environmental Concerns of Lithium Battery Production
The production of lithium batteries has significant environmental implications:
1. **Carbon Footprint**: The extraction and processing of raw materials contribute to greenhouse gas emissions.
2. **Resource Depletion**: The demand for lithium and other materials raises concerns about resource depletion and sustainability.
B. Recycling Processes
Recycling lithium batteries is crucial for minimizing environmental impact:
1. **Collection and Sorting**: Used batteries are collected and sorted for recycling.
2. **Recovery of Materials**: Advanced recycling processes recover valuable materials, such as lithium, cobalt, and nickel, for reuse.
3. **Reuse in New Battery Production**: Recycled materials can be reintegrated into the production of new batteries, promoting a circular economy.
VIII. Future Trends in Lithium Battery Production
A. Innovations in Materials and Technology
The future of lithium battery production is marked by exciting innovations:
1. **Solid-State Batteries**: These batteries use solid electrolytes, offering improved safety and energy density compared to traditional lithium-ion batteries.
2. **Alternative Chemistries**: Research is ongoing into alternative battery chemistries that could reduce reliance on scarce materials and enhance performance.
B. Sustainability Initiatives
Sustainability is becoming a key focus in battery production:
1. **Reducing Environmental Impact**: Manufacturers are exploring ways to minimize the carbon footprint of battery production through cleaner technologies and processes.
2. **Circular Economy in Battery Production**: Emphasizing recycling and material recovery helps create a more sustainable battery lifecycle.
IX. Conclusion
In summary, the production process of lithium batteries is a complex and multifaceted endeavor that involves careful sourcing of raw materials, precise manufacturing techniques, and rigorous testing protocols. Understanding this process is essential for consumers and industry stakeholders alike, as it sheds light on the importance of sustainability and responsible practices in battery production. As the demand for lithium batteries continues to grow, embracing innovative technologies and sustainable practices will be crucial for ensuring a greener future. By prioritizing these initiatives, we can contribute to a more sustainable energy landscape and support the transition to cleaner technologies.
Common Production Process of Lithium Batteries
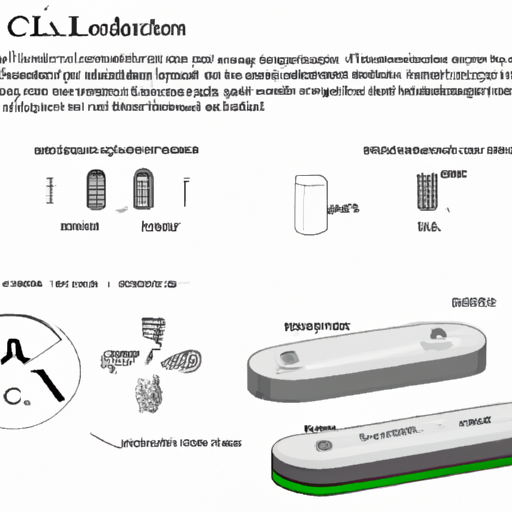
I. Introduction
Lithium batteries have become a cornerstone of modern technology, powering everything from smartphones and laptops to electric vehicles and renewable energy storage systems. Their lightweight, high energy density, and long cycle life make them the preferred choice for a wide range of applications across various industries. As the demand for energy storage solutions continues to rise, understanding the production process of lithium batteries is crucial for consumers, manufacturers, and policymakers alike. This article aims to educate readers on the common production process of lithium batteries, highlighting the significance of each step involved.
II. Understanding Lithium Batteries
A. Definition and Types of Lithium Batteries
Lithium batteries are rechargeable energy storage devices that utilize lithium ions to transfer energy between the anode and cathode during charging and discharging cycles. The two most common types of lithium batteries are:
1. **Lithium-ion (Li-ion) Batteries**: These batteries are widely used in consumer electronics and electric vehicles due to their high energy density and efficiency. They typically consist of a lithium cobalt oxide cathode and a graphite anode.
2. **Lithium Polymer (LiPo) Batteries**: LiPo batteries are known for their flexibility in shape and size, making them ideal for applications where space is limited, such as drones and wearable devices. They use a polymer electrolyte instead of a liquid electrolyte, allowing for a lighter and more compact design.
B. Key Components of Lithium Batteries
The main components of lithium batteries include:
1. **Anode**: The negative electrode, usually made of graphite, where lithium ions are stored during charging.
2. **Cathode**: The positive electrode, typically composed of lithium metal oxides, where lithium ions are released during discharge.
3. **Electrolyte**: A medium that allows the movement of lithium ions between the anode and cathode. It can be a liquid, gel, or solid.
4. **Separator**: A porous membrane that prevents direct contact between the anode and cathode while allowing lithium ions to pass through.
III. Raw Material Sourcing
A. Overview of Raw Materials
The production of lithium batteries begins with sourcing raw materials. Key materials include:
1. **Lithium Sources**: Lithium can be extracted from hard rock deposits (spodumene) or from brine sources found in salt flats. Each source has its own extraction and processing methods.
2. **Other Materials**: In addition to lithium, other essential materials include cobalt, nickel, and graphite. These materials contribute to the battery's performance and longevity.
B. Environmental and Ethical Considerations
The extraction of raw materials for lithium batteries raises environmental and ethical concerns. Mining practices can lead to habitat destruction, water depletion, and pollution. Additionally, the supply chain for materials like cobalt often involves labor practices that raise human rights concerns. As such, there is a growing emphasis on sourcing materials responsibly and ensuring supply chain transparency.
IV. Battery Cell Manufacturing Process
A. Electrode Preparation
The manufacturing process of lithium batteries involves several key steps:
1. **Mixing Active Materials**: The active materials for the anode and cathode are mixed with binders and solvents to create a slurry.
2. **Coating Processes**: The slurry is then coated onto metal foils (copper for the anode and aluminum for the cathode) to form thin films.
3. **Drying and Calendaring**: The coated films are dried to remove solvents and then compressed to achieve the desired thickness and density.
B. Cell Assembly
Once the electrodes are prepared, the next step is cell assembly:
1. **Stacking or Winding Electrodes**: The anode and cathode are either stacked or wound together with separators in between.
2. **Inserting Separators**: The separator is inserted to prevent short circuits while allowing lithium ions to pass through.
3. **Filling with Electrolyte**: The assembled cell is filled with electrolyte, which facilitates ion movement during charging and discharging.
C. Sealing and Packaging
The final step in cell manufacturing involves sealing and packaging:
1. **Cell Casing Options**: The cells are encased in protective materials, which can vary from cylindrical to prismatic shapes.
2. **Ensuring Safety and Integrity**: The sealing process is critical to prevent leakage and ensure the safety of the battery during operation.
V. Formation and Testing
A. Initial Formation Process
After assembly, the batteries undergo an initial formation process:
1. **Charging and Discharging Cycles**: The cells are subjected to several charging and discharging cycles to establish their performance characteristics.
2. **Establishing Battery Performance**: This process helps in determining the battery's capacity, voltage, and overall efficiency.
B. Quality Control Measures
Quality control is essential in battery production:
1. **Testing for Capacity, Voltage, and Safety**: Each battery is tested to ensure it meets the required specifications and safety standards.
2. **Identifying Defects and Ensuring Reliability**: Any defects are identified and addressed to ensure the reliability and longevity of the batteries.
VI. Battery Management Systems (BMS)
A. Role of BMS in Lithium Batteries
Battery Management Systems (BMS) play a crucial role in the operation of lithium batteries:
1. **Monitoring Battery Health**: BMS continuously monitors the state of charge, temperature, and overall health of the battery.
2. **Ensuring Safety During Operation**: The system prevents overcharging, overheating, and other conditions that could lead to battery failure or safety hazards.
B. Integration with Battery Production
The design and integration of BMS are essential for optimal battery performance:
1. **Designing BMS for Specific Applications**: BMS can be tailored to meet the specific needs of different applications, such as electric vehicles or renewable energy systems.
2. **Testing and Validation**: Rigorous testing ensures that the BMS functions correctly and enhances the safety and efficiency of the battery.
VII. Environmental Impact and Recycling
A. Environmental Concerns of Lithium Battery Production
The production of lithium batteries has significant environmental implications:
1. **Carbon Footprint**: The extraction and processing of raw materials contribute to greenhouse gas emissions.
2. **Resource Depletion**: The demand for lithium and other materials raises concerns about resource depletion and sustainability.
B. Recycling Processes
Recycling lithium batteries is crucial for minimizing environmental impact:
1. **Collection and Sorting**: Used batteries are collected and sorted for recycling.
2. **Recovery of Materials**: Advanced recycling processes recover valuable materials, such as lithium, cobalt, and nickel, for reuse.
3. **Reuse in New Battery Production**: Recycled materials can be reintegrated into the production of new batteries, promoting a circular economy.
VIII. Future Trends in Lithium Battery Production
A. Innovations in Materials and Technology
The future of lithium battery production is marked by exciting innovations:
1. **Solid-State Batteries**: These batteries use solid electrolytes, offering improved safety and energy density compared to traditional lithium-ion batteries.
2. **Alternative Chemistries**: Research is ongoing into alternative battery chemistries that could reduce reliance on scarce materials and enhance performance.
B. Sustainability Initiatives
Sustainability is becoming a key focus in battery production:
1. **Reducing Environmental Impact**: Manufacturers are exploring ways to minimize the carbon footprint of battery production through cleaner technologies and processes.
2. **Circular Economy in Battery Production**: Emphasizing recycling and material recovery helps create a more sustainable battery lifecycle.
IX. Conclusion
In summary, the production process of lithium batteries is a complex and multifaceted endeavor that involves careful sourcing of raw materials, precise manufacturing techniques, and rigorous testing protocols. Understanding this process is essential for consumers and industry stakeholders alike, as it sheds light on the importance of sustainability and responsible practices in battery production. As the demand for lithium batteries continues to grow, embracing innovative technologies and sustainable practices will be crucial for ensuring a greener future. By prioritizing these initiatives, we can contribute to a more sustainable energy landscape and support the transition to cleaner technologies.