What is the Product of Battery Mold?
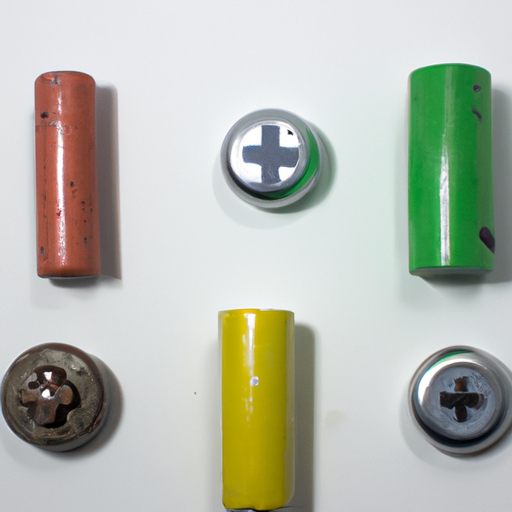
I. Introduction
In the rapidly evolving world of technology, batteries have become an essential component of our daily lives, powering everything from smartphones to electric vehicles. At the heart of battery production lies a crucial element known as the battery mold. This article aims to explore the significance of battery molds in the manufacturing process, their types, materials, innovations, challenges, and future trends. By understanding battery molds, we can appreciate their role in enhancing battery performance and sustainability.
II. Understanding Battery Molds
A. What are Battery Molds?
Battery molds are specialized tools used in the manufacturing of battery components. They are designed to shape and form various parts of batteries, ensuring that each component meets precise specifications. Battery molds can be categorized into different types based on the battery technology they support, such as lead-acid and lithium-ion batteries.
1. Description of Battery Molds
Battery molds are typically made from durable materials that can withstand high temperatures and pressures during the manufacturing process. They are engineered to create specific shapes and sizes, which are critical for the performance and efficiency of the batteries.
2. Types of Battery Molds
Lead-Acid Molds: These molds are used in the production of lead-acid batteries, which are commonly found in vehicles. They are designed to create the lead plates and separators that are essential for the battery's function.
Lithium-Ion Molds: With the rise of electric vehicles and portable electronics, lithium-ion batteries have gained prominence. Molds for these batteries are designed to create components like the battery casing and electrode structures.
B. Materials Used in Battery Molds
The choice of materials for battery molds is critical to their performance and longevity.
1. Common Materials
Steel: Known for its strength and durability, steel is often used for molds that require high precision and can withstand repeated use.
Aluminum: Lightweight and resistant to corrosion, aluminum molds are favored for their ease of handling and cost-effectiveness.
Plastic: In some cases, plastic molds are used for lower-cost applications, especially in the production of smaller battery components.
2. Properties Required for Battery Mold Materials
The materials used in battery molds must possess specific properties, including:
Thermal Resistance: Molds must withstand high temperatures during the manufacturing process without deforming.
Durability: Given the repetitive nature of battery production, molds need to be robust and long-lasting.
Precision: High precision is essential to ensure that battery components fit together correctly, which directly impacts battery performance.
III. The Role of Battery Molds in Battery Production
A. The Manufacturing Process of Batteries
The production of batteries involves several stages, including material preparation, component shaping, assembly, and testing. Battery molds play a pivotal role in shaping the components during the manufacturing process.
1. Overview of Battery Production Stages
Material Preparation: Raw materials are processed and prepared for use in battery components.
Component Shaping: This is where battery molds come into play, shaping materials into the required forms.
Assembly: Shaped components are assembled into complete battery units.
Testing: Finished batteries undergo rigorous testing to ensure they meet performance standards.
2. The Specific Role of Molds in Shaping Battery Components
Molds are used to create various battery components, including casings, electrodes, and separators. The precision of these molds ensures that each component fits perfectly, which is crucial for the overall efficiency and safety of the battery.
B. Importance of Precision and Quality in Battery Molds
1. Impact on Battery Performance and Lifespan
The quality of battery molds directly affects the performance and lifespan of the batteries produced. High-quality molds lead to better-fitting components, which can enhance energy efficiency and reduce the risk of failure.
2. Consequences of Poor Mold Quality
Conversely, poor-quality molds can result in defects, leading to reduced battery performance, shorter lifespans, and potential safety hazards. This underscores the importance of investing in high-quality mold production.
IV. Types of Battery Molds
A. Injection Molds
1. Description and Applications
Injection molds are used to inject molten material into a mold cavity, allowing for the creation of complex shapes. They are commonly used in the production of battery casings and other intricate components.
2. Advantages and Disadvantages
Advantages: High precision, ability to produce complex shapes, and efficient production rates.
Disadvantages: Higher initial costs and longer lead times for mold production.
B. Compression Molds
1. Description and Applications
Compression molds involve placing material into a heated mold cavity, where it is compressed to form the desired shape. This method is often used for larger battery components.
2. Advantages and Disadvantages
Advantages: Simplicity of the process and lower costs for larger parts.
Disadvantages: Limited complexity in shapes and longer cycle times.
C. Blow Molds
1. Description and Applications
Blow molds are used to create hollow components by inflating a heated plastic tube within a mold. This method is often used for producing battery casings.
2. Advantages and Disadvantages
Advantages: Efficient for producing hollow shapes and lightweight components.
Disadvantages: Limited to specific materials and shapes.
V. Innovations in Battery Mold Technology
A. Advances in Mold Design and Manufacturing
1. Use of Computer-Aided Design (CAD) and Simulation
Modern mold design increasingly relies on CAD software, allowing for precise modeling and simulation of the molding process. This technology helps manufacturers optimize mold designs for better performance.
2. 3D Printing in Mold Production
3D printing is revolutionizing mold production by enabling rapid prototyping and the creation of complex geometries that were previously difficult to achieve. This innovation reduces lead times and costs.
B. Eco-Friendly Materials and Processes
1. Sustainable Practices in Battery Mold Manufacturing
As environmental concerns grow, manufacturers are exploring sustainable practices in mold production. This includes using recycled materials and reducing waste during the manufacturing process.
2. Impact on the Environment and Battery Lifecycle
Eco-friendly practices not only benefit the environment but also enhance the overall sustainability of battery production, contributing to a greener battery lifecycle.
VI. Challenges in Battery Mold Production
A. Technical Challenges
1. Complexity of Battery Designs
As battery technology advances, the designs become more complex, posing challenges for mold manufacturers to create molds that can accommodate these intricate designs.
2. Need for High Precision and Durability
The demand for high precision and durability in molds requires continuous innovation and investment in advanced manufacturing techniques.
B. Economic Challenges
1. Cost of Materials and Production
The rising costs of raw materials and production can impact the overall profitability of battery mold manufacturing, necessitating efficient resource management.
2. Market Demand and Competition
The growing demand for batteries, particularly in the electric vehicle market, has intensified competition among manufacturers, pushing them to innovate and reduce costs.
VII. Future Trends in Battery Mold Development
A. Emerging Technologies in Battery Production
1. Solid-State Batteries and Their Implications for Mold Design
The development of solid-state batteries presents new challenges and opportunities for mold design, as these batteries require different manufacturing processes and materials.
2. The Role of Automation and Robotics
Automation and robotics are increasingly being integrated into mold production, enhancing efficiency and precision while reducing labor costs.
B. Predictions for the Battery Mold Market
1. Growth Opportunities and Potential Challenges
The battery mold market is expected to grow significantly, driven by the increasing demand for batteries in various applications. However, manufacturers must navigate challenges related to material costs and technological advancements.
2. The Impact of Global Energy Trends on Battery Production
As the world shifts towards renewable energy sources, the demand for efficient and sustainable battery production will continue to rise, influencing the development of battery molds.
VIII. Conclusion
Battery molds play a vital role in the manufacturing process of batteries, impacting their performance, efficiency, and sustainability. As technology continues to advance, the importance of high-quality molds will only increase. The future of battery mold technology looks promising, with innovations in design, materials, and production processes paving the way for more efficient and eco-friendly battery manufacturing. As we move forward, further research and innovation in this field will be essential to meet the growing demands of the battery industry.
IX. References
A comprehensive list of academic papers, articles, and resources for further reading on battery molds and manufacturing processes can be provided upon request.
What is the Product of Battery Mold?
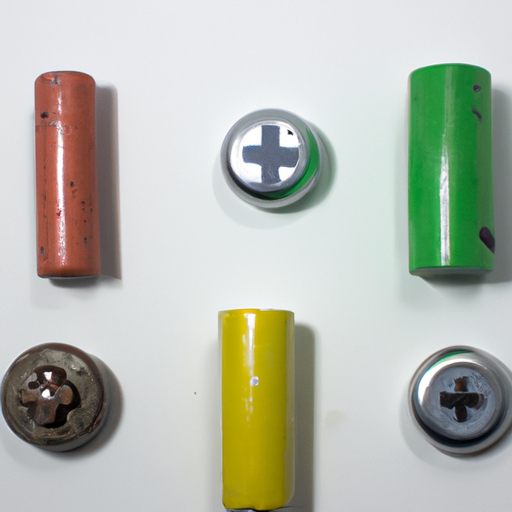
I. Introduction
In the rapidly evolving world of technology, batteries have become an essential component of our daily lives, powering everything from smartphones to electric vehicles. At the heart of battery production lies a crucial element known as the battery mold. This article aims to explore the significance of battery molds in the manufacturing process, their types, materials, innovations, challenges, and future trends. By understanding battery molds, we can appreciate their role in enhancing battery performance and sustainability.
II. Understanding Battery Molds
A. What are Battery Molds?
Battery molds are specialized tools used in the manufacturing of battery components. They are designed to shape and form various parts of batteries, ensuring that each component meets precise specifications. Battery molds can be categorized into different types based on the battery technology they support, such as lead-acid and lithium-ion batteries.
1. Description of Battery Molds
Battery molds are typically made from durable materials that can withstand high temperatures and pressures during the manufacturing process. They are engineered to create specific shapes and sizes, which are critical for the performance and efficiency of the batteries.
2. Types of Battery Molds
Lead-Acid Molds: These molds are used in the production of lead-acid batteries, which are commonly found in vehicles. They are designed to create the lead plates and separators that are essential for the battery's function.
Lithium-Ion Molds: With the rise of electric vehicles and portable electronics, lithium-ion batteries have gained prominence. Molds for these batteries are designed to create components like the battery casing and electrode structures.
B. Materials Used in Battery Molds
The choice of materials for battery molds is critical to their performance and longevity.
1. Common Materials
Steel: Known for its strength and durability, steel is often used for molds that require high precision and can withstand repeated use.
Aluminum: Lightweight and resistant to corrosion, aluminum molds are favored for their ease of handling and cost-effectiveness.
Plastic: In some cases, plastic molds are used for lower-cost applications, especially in the production of smaller battery components.
2. Properties Required for Battery Mold Materials
The materials used in battery molds must possess specific properties, including:
Thermal Resistance: Molds must withstand high temperatures during the manufacturing process without deforming.
Durability: Given the repetitive nature of battery production, molds need to be robust and long-lasting.
Precision: High precision is essential to ensure that battery components fit together correctly, which directly impacts battery performance.
III. The Role of Battery Molds in Battery Production
A. The Manufacturing Process of Batteries
The production of batteries involves several stages, including material preparation, component shaping, assembly, and testing. Battery molds play a pivotal role in shaping the components during the manufacturing process.
1. Overview of Battery Production Stages
Material Preparation: Raw materials are processed and prepared for use in battery components.
Component Shaping: This is where battery molds come into play, shaping materials into the required forms.
Assembly: Shaped components are assembled into complete battery units.
Testing: Finished batteries undergo rigorous testing to ensure they meet performance standards.
2. The Specific Role of Molds in Shaping Battery Components
Molds are used to create various battery components, including casings, electrodes, and separators. The precision of these molds ensures that each component fits perfectly, which is crucial for the overall efficiency and safety of the battery.
B. Importance of Precision and Quality in Battery Molds
1. Impact on Battery Performance and Lifespan
The quality of battery molds directly affects the performance and lifespan of the batteries produced. High-quality molds lead to better-fitting components, which can enhance energy efficiency and reduce the risk of failure.
2. Consequences of Poor Mold Quality
Conversely, poor-quality molds can result in defects, leading to reduced battery performance, shorter lifespans, and potential safety hazards. This underscores the importance of investing in high-quality mold production.
IV. Types of Battery Molds
A. Injection Molds
1. Description and Applications
Injection molds are used to inject molten material into a mold cavity, allowing for the creation of complex shapes. They are commonly used in the production of battery casings and other intricate components.
2. Advantages and Disadvantages
Advantages: High precision, ability to produce complex shapes, and efficient production rates.
Disadvantages: Higher initial costs and longer lead times for mold production.
B. Compression Molds
1. Description and Applications
Compression molds involve placing material into a heated mold cavity, where it is compressed to form the desired shape. This method is often used for larger battery components.
2. Advantages and Disadvantages
Advantages: Simplicity of the process and lower costs for larger parts.
Disadvantages: Limited complexity in shapes and longer cycle times.
C. Blow Molds
1. Description and Applications
Blow molds are used to create hollow components by inflating a heated plastic tube within a mold. This method is often used for producing battery casings.
2. Advantages and Disadvantages
Advantages: Efficient for producing hollow shapes and lightweight components.
Disadvantages: Limited to specific materials and shapes.
V. Innovations in Battery Mold Technology
A. Advances in Mold Design and Manufacturing
1. Use of Computer-Aided Design (CAD) and Simulation
Modern mold design increasingly relies on CAD software, allowing for precise modeling and simulation of the molding process. This technology helps manufacturers optimize mold designs for better performance.
2. 3D Printing in Mold Production
3D printing is revolutionizing mold production by enabling rapid prototyping and the creation of complex geometries that were previously difficult to achieve. This innovation reduces lead times and costs.
B. Eco-Friendly Materials and Processes
1. Sustainable Practices in Battery Mold Manufacturing
As environmental concerns grow, manufacturers are exploring sustainable practices in mold production. This includes using recycled materials and reducing waste during the manufacturing process.
2. Impact on the Environment and Battery Lifecycle
Eco-friendly practices not only benefit the environment but also enhance the overall sustainability of battery production, contributing to a greener battery lifecycle.
VI. Challenges in Battery Mold Production
A. Technical Challenges
1. Complexity of Battery Designs
As battery technology advances, the designs become more complex, posing challenges for mold manufacturers to create molds that can accommodate these intricate designs.
2. Need for High Precision and Durability
The demand for high precision and durability in molds requires continuous innovation and investment in advanced manufacturing techniques.
B. Economic Challenges
1. Cost of Materials and Production
The rising costs of raw materials and production can impact the overall profitability of battery mold manufacturing, necessitating efficient resource management.
2. Market Demand and Competition
The growing demand for batteries, particularly in the electric vehicle market, has intensified competition among manufacturers, pushing them to innovate and reduce costs.
VII. Future Trends in Battery Mold Development
A. Emerging Technologies in Battery Production
1. Solid-State Batteries and Their Implications for Mold Design
The development of solid-state batteries presents new challenges and opportunities for mold design, as these batteries require different manufacturing processes and materials.
2. The Role of Automation and Robotics
Automation and robotics are increasingly being integrated into mold production, enhancing efficiency and precision while reducing labor costs.
B. Predictions for the Battery Mold Market
1. Growth Opportunities and Potential Challenges
The battery mold market is expected to grow significantly, driven by the increasing demand for batteries in various applications. However, manufacturers must navigate challenges related to material costs and technological advancements.
2. The Impact of Global Energy Trends on Battery Production
As the world shifts towards renewable energy sources, the demand for efficient and sustainable battery production will continue to rise, influencing the development of battery molds.
VIII. Conclusion
Battery molds play a vital role in the manufacturing process of batteries, impacting their performance, efficiency, and sustainability. As technology continues to advance, the importance of high-quality molds will only increase. The future of battery mold technology looks promising, with innovations in design, materials, and production processes paving the way for more efficient and eco-friendly battery manufacturing. As we move forward, further research and innovation in this field will be essential to meet the growing demands of the battery industry.
IX. References
A comprehensive list of academic papers, articles, and resources for further reading on battery molds and manufacturing processes can be provided upon request.