Latest Battery Holder Welding Specifications
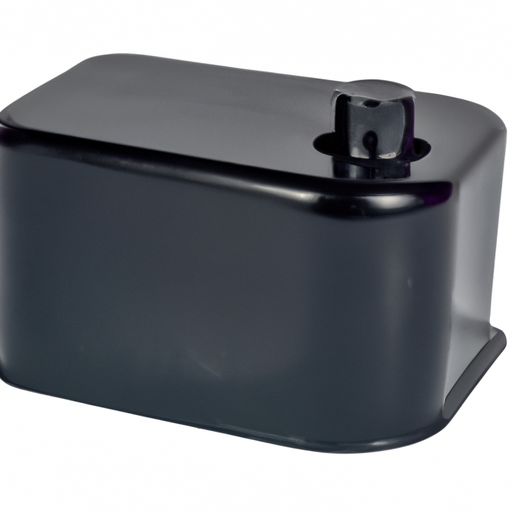
I. Introduction
In the rapidly evolving landscape of modern technology, the significance of battery holder welding cannot be overstated. As the demand for efficient and reliable energy storage solutions continues to rise, the manufacturing processes that support these technologies must also advance. This document aims to provide a comprehensive overview of the latest specifications in battery holder welding, exploring the techniques, materials, and quality control measures that are shaping the industry today. Additionally, we will touch upon the evolution of welding techniques in battery holder manufacturing, highlighting how innovation has driven improvements in performance and reliability.
II. Understanding Battery Holders
Battery holders are essential components in the realm of energy storage, serving as the interface between batteries and electronic devices. Their primary function is to securely house batteries while ensuring optimal electrical connectivity. Battery holders come in various forms, including cylindrical, prismatic, and pouch types, each designed to accommodate specific battery shapes and sizes.
The materials used in battery holder construction are critical to their performance. Common materials include plastics, metals, and composites, each chosen for their unique properties such as conductivity, thermal resistance, and mechanical strength. Understanding these materials is crucial for manufacturers aiming to produce high-quality battery holders that meet the demands of modern applications.
III. Welding Techniques for Battery Holders
The welding of battery holders involves several techniques, each with its own advantages and applications.
A. Overview of Welding Methods
1. **Resistance Welding**: This method uses heat generated by electrical resistance to join materials. It is widely used for its speed and efficiency, making it ideal for high-volume production.
2. **Laser Welding**: Utilizing focused laser beams, this technique allows for precise and clean welds. It is particularly beneficial for thin materials and complex geometries.
3. **Ultrasonic Welding**: This method employs high-frequency ultrasonic vibrations to create a bond between materials. It is often used for thermoplastics and is known for its speed and low energy consumption.
4. **Spot Welding**: A form of resistance welding, spot welding involves joining two or more pieces of metal at specific points. It is commonly used in battery holder manufacturing due to its effectiveness in creating strong joints.
B. Comparison of Techniques
When comparing these welding techniques, several factors come into play, including application suitability, efficiency, and cost. Resistance welding is favored for its speed and ability to handle large volumes, while laser welding offers precision for intricate designs. Ultrasonic welding is lauded for its energy efficiency, and spot welding remains a staple for its simplicity and effectiveness. Manufacturers must carefully consider these factors when selecting the appropriate welding method for their battery holders.
IV. Latest Specifications in Battery Holder Welding
A. Industry Standards and Regulations
Adhering to industry standards is paramount in battery holder welding. The International Electrotechnical Commission (IEC) and the American National Standards Institute (ANSI) provide guidelines that ensure safety, reliability, and performance. These standards cover various aspects of battery holder design and manufacturing, including welding processes.
B. Material Specifications
The materials used in battery holder construction must meet specific specifications to ensure optimal performance. Key considerations include:
1. **Conductivity Requirements**: Materials must exhibit high electrical conductivity to minimize energy loss during operation.
2. **Thermal Properties**: Battery holders must withstand temperature fluctuations without compromising structural integrity.
3. **Mechanical Strength**: The joints created during welding must possess sufficient strength to endure mechanical stresses during use.
C. Joint Design Specifications
The design of welded joints is critical to the overall performance of battery holders. Various joint types, such as lap joints and butt joints, are employed based on the application. Recommended joint configurations are developed to optimize performance, ensuring that the welded areas can withstand the rigors of use while maintaining electrical connectivity.
V. Quality Control in Battery Holder Welding
A. Importance of Quality Assurance
Quality assurance is a vital component of the welding process. Ensuring that welded joints meet established specifications is crucial for the reliability and safety of battery holders.
B. Testing Methods for Welded Joints
Several testing methods are employed to assess the quality of welded joints:
1. **Visual Inspection**: A preliminary assessment that identifies obvious defects such as misalignment or surface irregularities.
2. **Non-Destructive Testing (NDT)**: Techniques such as ultrasonic testing and X-ray inspection allow for the evaluation of weld integrity without damaging the components.
3. **Destructive Testing Methods**: These methods involve subjecting welded joints to stress until failure, providing valuable data on their strength and durability.
C. Common Defects and Their Implications
Common defects in battery holder welding include incomplete fusion, porosity, and cracks. These issues can lead to reduced performance, increased resistance, and potential failure of the battery holder. Identifying and addressing these defects through rigorous quality control measures is essential for maintaining product integrity.
VI. Innovations and Trends in Battery Holder Welding
A. Advances in Welding Technology
The welding landscape is continually evolving, with several innovations shaping the future of battery holder manufacturing:
1. **Automation and Robotics**: The integration of automated systems and robotics in welding processes enhances precision, reduces labor costs, and increases production efficiency.
2. **Smart Welding Systems**: Real-time monitoring and feedback systems are being developed to optimize welding parameters, ensuring consistent quality and performance.
B. Sustainability Considerations
As the industry moves towards more sustainable practices, eco-friendly materials and processes are gaining traction. Manufacturers are exploring recycling and waste management practices to minimize their environmental impact, aligning with global sustainability goals.
VII. Case Studies
Examining successful implementations of advanced welding techniques in battery holder production provides valuable insights. Industry leaders have adopted innovative methods that not only enhance product quality but also streamline production processes. These case studies highlight the importance of continuous improvement and adaptation in a competitive market.
VIII. Conclusion
In summary, the latest specifications in battery holder welding encompass a wide range of techniques, materials, and quality control measures. As technology continues to advance, manufacturers must stay informed about industry standards and best practices to ensure the reliability and performance of their products. The future of battery holder welding looks promising, with ongoing innovations paving the way for more efficient and sustainable manufacturing processes. Industry stakeholders are encouraged to adopt these best practices to remain competitive and meet the growing demands of the energy storage market.
IX. References
A comprehensive list of academic papers, industry reports, and standards referenced in this document will provide readers with additional resources for further exploration of battery holder welding specifications. These references will serve as a foundation for understanding the complexities and advancements in this critical area of manufacturing.
---
This blog post provides a detailed exploration of the latest battery holder welding specifications, ensuring a thorough understanding of the topic while maintaining a professional and informative tone.
Latest Battery Holder Welding Specifications
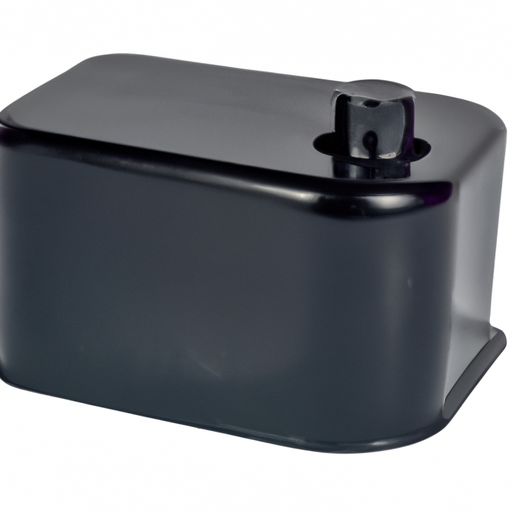
I. Introduction
In the rapidly evolving landscape of modern technology, the significance of battery holder welding cannot be overstated. As the demand for efficient and reliable energy storage solutions continues to rise, the manufacturing processes that support these technologies must also advance. This document aims to provide a comprehensive overview of the latest specifications in battery holder welding, exploring the techniques, materials, and quality control measures that are shaping the industry today. Additionally, we will touch upon the evolution of welding techniques in battery holder manufacturing, highlighting how innovation has driven improvements in performance and reliability.
II. Understanding Battery Holders
Battery holders are essential components in the realm of energy storage, serving as the interface between batteries and electronic devices. Their primary function is to securely house batteries while ensuring optimal electrical connectivity. Battery holders come in various forms, including cylindrical, prismatic, and pouch types, each designed to accommodate specific battery shapes and sizes.
The materials used in battery holder construction are critical to their performance. Common materials include plastics, metals, and composites, each chosen for their unique properties such as conductivity, thermal resistance, and mechanical strength. Understanding these materials is crucial for manufacturers aiming to produce high-quality battery holders that meet the demands of modern applications.
III. Welding Techniques for Battery Holders
The welding of battery holders involves several techniques, each with its own advantages and applications.
A. Overview of Welding Methods
1. **Resistance Welding**: This method uses heat generated by electrical resistance to join materials. It is widely used for its speed and efficiency, making it ideal for high-volume production.
2. **Laser Welding**: Utilizing focused laser beams, this technique allows for precise and clean welds. It is particularly beneficial for thin materials and complex geometries.
3. **Ultrasonic Welding**: This method employs high-frequency ultrasonic vibrations to create a bond between materials. It is often used for thermoplastics and is known for its speed and low energy consumption.
4. **Spot Welding**: A form of resistance welding, spot welding involves joining two or more pieces of metal at specific points. It is commonly used in battery holder manufacturing due to its effectiveness in creating strong joints.
B. Comparison of Techniques
When comparing these welding techniques, several factors come into play, including application suitability, efficiency, and cost. Resistance welding is favored for its speed and ability to handle large volumes, while laser welding offers precision for intricate designs. Ultrasonic welding is lauded for its energy efficiency, and spot welding remains a staple for its simplicity and effectiveness. Manufacturers must carefully consider these factors when selecting the appropriate welding method for their battery holders.
IV. Latest Specifications in Battery Holder Welding
A. Industry Standards and Regulations
Adhering to industry standards is paramount in battery holder welding. The International Electrotechnical Commission (IEC) and the American National Standards Institute (ANSI) provide guidelines that ensure safety, reliability, and performance. These standards cover various aspects of battery holder design and manufacturing, including welding processes.
B. Material Specifications
The materials used in battery holder construction must meet specific specifications to ensure optimal performance. Key considerations include:
1. **Conductivity Requirements**: Materials must exhibit high electrical conductivity to minimize energy loss during operation.
2. **Thermal Properties**: Battery holders must withstand temperature fluctuations without compromising structural integrity.
3. **Mechanical Strength**: The joints created during welding must possess sufficient strength to endure mechanical stresses during use.
C. Joint Design Specifications
The design of welded joints is critical to the overall performance of battery holders. Various joint types, such as lap joints and butt joints, are employed based on the application. Recommended joint configurations are developed to optimize performance, ensuring that the welded areas can withstand the rigors of use while maintaining electrical connectivity.
V. Quality Control in Battery Holder Welding
A. Importance of Quality Assurance
Quality assurance is a vital component of the welding process. Ensuring that welded joints meet established specifications is crucial for the reliability and safety of battery holders.
B. Testing Methods for Welded Joints
Several testing methods are employed to assess the quality of welded joints:
1. **Visual Inspection**: A preliminary assessment that identifies obvious defects such as misalignment or surface irregularities.
2. **Non-Destructive Testing (NDT)**: Techniques such as ultrasonic testing and X-ray inspection allow for the evaluation of weld integrity without damaging the components.
3. **Destructive Testing Methods**: These methods involve subjecting welded joints to stress until failure, providing valuable data on their strength and durability.
C. Common Defects and Their Implications
Common defects in battery holder welding include incomplete fusion, porosity, and cracks. These issues can lead to reduced performance, increased resistance, and potential failure of the battery holder. Identifying and addressing these defects through rigorous quality control measures is essential for maintaining product integrity.
VI. Innovations and Trends in Battery Holder Welding
A. Advances in Welding Technology
The welding landscape is continually evolving, with several innovations shaping the future of battery holder manufacturing:
1. **Automation and Robotics**: The integration of automated systems and robotics in welding processes enhances precision, reduces labor costs, and increases production efficiency.
2. **Smart Welding Systems**: Real-time monitoring and feedback systems are being developed to optimize welding parameters, ensuring consistent quality and performance.
B. Sustainability Considerations
As the industry moves towards more sustainable practices, eco-friendly materials and processes are gaining traction. Manufacturers are exploring recycling and waste management practices to minimize their environmental impact, aligning with global sustainability goals.
VII. Case Studies
Examining successful implementations of advanced welding techniques in battery holder production provides valuable insights. Industry leaders have adopted innovative methods that not only enhance product quality but also streamline production processes. These case studies highlight the importance of continuous improvement and adaptation in a competitive market.
VIII. Conclusion
In summary, the latest specifications in battery holder welding encompass a wide range of techniques, materials, and quality control measures. As technology continues to advance, manufacturers must stay informed about industry standards and best practices to ensure the reliability and performance of their products. The future of battery holder welding looks promising, with ongoing innovations paving the way for more efficient and sustainable manufacturing processes. Industry stakeholders are encouraged to adopt these best practices to remain competitive and meet the growing demands of the energy storage market.
IX. References
A comprehensive list of academic papers, industry reports, and standards referenced in this document will provide readers with additional resources for further exploration of battery holder welding specifications. These references will serve as a foundation for understanding the complexities and advancements in this critical area of manufacturing.
---
This blog post provides a detailed exploration of the latest battery holder welding specifications, ensuring a thorough understanding of the topic while maintaining a professional and informative tone.