What is the Mainstream CR2450 Battery Holder Production Process?
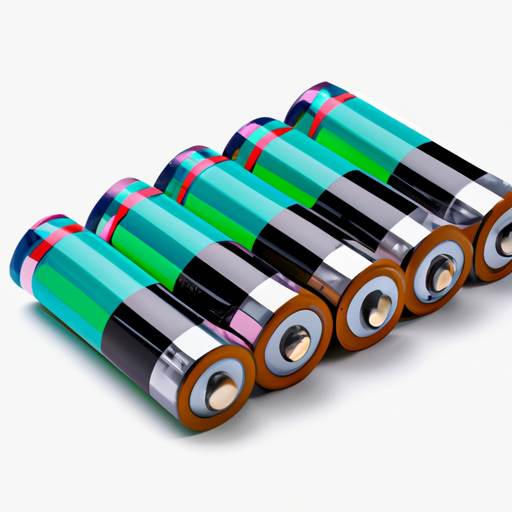
I. Introduction
A. Overview of CR2450 Batteries
CR2450 batteries are a type of lithium coin cell battery, widely recognized for their compact size and high energy density. Measuring 24mm in diameter and 5mm in thickness, these batteries typically provide a nominal voltage of 3 volts. They are commonly used in various electronic devices, including watches, calculators, medical devices, and remote controls, due to their long shelf life and reliability.
B. Importance of Battery Holders
Battery holders play a crucial role in the functionality of electronic devices. They not only secure the battery in place but also ensure proper electrical contact between the battery and the device. The design of battery holders must consider factors such as ease of battery replacement, compatibility with different battery types, and the overall aesthetics of the device. A well-designed battery holder enhances the user experience and contributes to the longevity of the device.
C. Purpose of the Article
This article aims to explore the production process of CR2450 battery holders, detailing the steps involved from material selection to quality control. Understanding this process is essential for manufacturers and consumers alike, as it highlights the complexities and considerations involved in producing a seemingly simple component.
II. Understanding CR2450 Battery Holders
A. Design and Structure
The design of CR2450 battery holders is critical for their functionality. Typically made from a combination of plastic and metal, these holders must provide both durability and conductivity. The plastic components often serve as the housing, while metal contacts ensure a reliable electrical connection.
1. Materials Used
Common materials for battery holders include polycarbonate and ABS plastic for the housing, and nickel-plated steel or brass for the contact points. The choice of materials is influenced by factors such as cost, weight, and electrical conductivity.
2. Types of Battery Holders
Battery holders can be categorized into several types, including snap-in holders, screw-mounted holders, and solderable holders. Each type has its specific applications and advantages, depending on the design requirements of the electronic device.
B. Key Features
1. Contact Points
The contact points in a battery holder are designed to ensure a secure connection with the battery terminals. These points must be engineered to withstand repeated insertions and removals without losing their conductive properties.
2. Retention Mechanisms
Retention mechanisms are essential for keeping the battery securely in place. Common designs include spring-loaded contacts and clips that hold the battery firmly, preventing it from rattling or disconnecting during use.
3. Size and Compatibility
The size of the battery holder must match the dimensions of the CR2450 battery, ensuring a snug fit. Additionally, compatibility with various electronic devices is crucial, as manufacturers often design holders that can accommodate multiple battery types.
III. The Production Process of CR2450 Battery Holders
A. Material Selection
The first step in the production process is material selection. Manufacturers must choose materials that meet the functional requirements of the battery holder while also considering cost-effectiveness and availability.
1. Types of Materials
As mentioned earlier, plastic and metal are the primary materials used in battery holders. The plastic components provide insulation and structural integrity, while the metal contacts ensure electrical conductivity.
2. Criteria for Material Selection
Key criteria for material selection include mechanical strength, thermal stability, and resistance to corrosion. Manufacturers often conduct tests to evaluate the performance of different materials under various conditions.
B. Design and Prototyping
Once materials are selected, the design phase begins. This involves creating detailed models of the battery holder using Computer-Aided Design (CAD) software.
1. CAD Modeling
CAD modeling allows designers to visualize the battery holder's structure and make necessary adjustments before moving to production. This step is crucial for identifying potential design flaws and ensuring that the holder meets all specifications.
2. Prototyping Techniques
Prototyping techniques such as 3D printing and CNC machining are employed to create physical models of the battery holder. These prototypes are tested for fit and functionality, providing valuable insights that inform the final design.
C. Manufacturing Techniques
The manufacturing of CR2450 battery holders involves several techniques, each with its advantages and disadvantages.
1. Injection Molding
Injection molding is one of the most common methods for producing plastic components of battery holders.
a. Process Overview
In this process, molten plastic is injected into a mold, where it cools and solidifies into the desired shape. This method is highly efficient for mass production, allowing for consistent quality and rapid output.
b. Advantages and Disadvantages
The primary advantage of injection molding is its ability to produce complex shapes with high precision. However, the initial setup costs for molds can be significant, making it less economical for small production runs.
2. Stamping and Forming
For the metal components, stamping and forming techniques are often used.
a. Process Overview
In stamping, sheets of metal are cut and shaped into the required forms using dies. This method is suitable for producing high volumes of metal parts quickly and accurately.
b. Applications in Battery Holder Production
Stamping is particularly useful for creating the contact points of battery holders, ensuring they maintain their shape and conductivity over time.
3. Assembly Processes
After the individual components are manufactured, they must be assembled into the final product.
a. Manual vs. Automated Assembly
Assembly can be done manually or through automated processes. Automated assembly lines are increasingly common, as they enhance efficiency and reduce labor costs.
b. Quality Control Measures
Quality control is essential during assembly to ensure that each battery holder meets the required specifications. This may involve visual inspections, dimensional checks, and functional testing.
D. Surface Treatment and Finishing
The final step in the production process involves surface treatment and finishing.
1. Coating Options
Surface treatments such as plating or painting are applied to enhance the durability and appearance of the battery holder. Nickel plating, for example, can improve corrosion resistance and conductivity.
2. Importance of Surface Treatment for Durability
Proper surface treatment is crucial for ensuring that the battery holder can withstand environmental factors such as humidity and temperature fluctuations, which can affect performance over time.
IV. Quality Control in Production
A. Importance of Quality Assurance
Quality assurance is a critical aspect of the production process, ensuring that each battery holder meets industry standards and customer expectations.
B. Testing Methods
Various testing methods are employed to assess the quality of battery holders.
1. Dimensional Checks
Dimensional checks verify that the battery holder's size and shape conform to specifications, ensuring a proper fit for the CR2450 battery.
2. Functional Testing
Functional testing assesses the electrical performance of the battery holder, ensuring that it provides a reliable connection with the battery.
3. Environmental Testing
Environmental testing evaluates the battery holder's performance under different conditions, such as extreme temperatures and humidity levels.
C. Compliance with Industry Standards
Manufacturers must comply with industry standards to ensure the safety and reliability of their products.
1. ISO Certifications
ISO certifications demonstrate that a manufacturer adheres to international quality management standards, providing assurance to customers regarding product quality.
2. Safety Regulations
Compliance with safety regulations is essential, particularly for battery holders used in medical devices and consumer electronics.
V. Challenges in the Production Process
A. Material Sourcing Issues
Sourcing high-quality materials can be challenging, particularly in times of supply chain disruptions. Manufacturers must establish reliable relationships with suppliers to ensure consistent quality.
B. Technological Advancements
Keeping up with technological advancements is crucial for manufacturers to remain competitive. This includes adopting new manufacturing techniques and materials that enhance product performance.
C. Market Demand Fluctuations
Market demand for CR2450 battery holders can fluctuate, impacting production volumes. Manufacturers must be agile in their production processes to respond to changing market conditions.
D. Environmental Considerations
Sustainability is becoming increasingly important in manufacturing. Companies must consider the environmental impact of their production processes and seek ways to minimize waste and energy consumption.
VI. Future Trends in Battery Holder Production
A. Innovations in Materials and Design
The future of battery holder production will likely see innovations in materials, such as the use of biodegradable plastics and advanced composites that offer improved performance and sustainability.
B. Automation and Industry 4.0
The integration of automation and Industry 4.0 technologies will enhance production efficiency, allowing manufacturers to produce battery holders with greater precision and speed.
C. Sustainability Practices in Production
Sustainability practices, such as recycling and waste reduction, will become increasingly important as manufacturers seek to minimize their environmental footprint.
VII. Conclusion
A. Recap of the CR2450 Battery Holder Production Process
The production process of CR2450 battery holders involves several critical steps, from material selection and design to manufacturing and quality control. Each stage plays a vital role in ensuring the final product meets the required specifications and performance standards.
B. The Significance of Quality and Innovation in the Industry
Quality and innovation are paramount in the battery holder manufacturing industry. As technology advances and consumer demands evolve, manufacturers must continuously improve their processes and products to remain competitive.
C. Final Thoughts on the Future of Battery Holder Manufacturing
The future of battery holder manufacturing looks promising, with advancements in materials, automation, and sustainability practices paving the way for more efficient and environmentally friendly production processes. As the demand for reliable and high-performance battery holders continues to grow, manufacturers must adapt and innovate to meet the challenges ahead.
VIII. References
A. Citing Relevant Literature and Sources
1. Battery University. (n.d.). "Battery Basics." Retrieved from [Battery University](https://batteryuniversity.com)
2. ISO. (n.d.). "ISO 9001:2015 - Quality Management Systems." Retrieved from [ISO](https://www.iso.org)
3. Electronics Weekly. (2021). "The Future of Battery Technology." Retrieved from [Electronics Weekly](https://www.electronicsweekly.com)
B. Additional Resources for Further Reading
1. "The Complete Guide to Battery Holders" - A comprehensive resource on battery holder design and applications.
2. "Advancements in Battery Technology" - An exploration of the latest trends and innovations in battery technology.
This blog post provides a detailed overview of the production process of CR2450 battery holders, highlighting the complexities and considerations involved in manufacturing this essential component.
What is the Mainstream CR2450 Battery Holder Production Process?
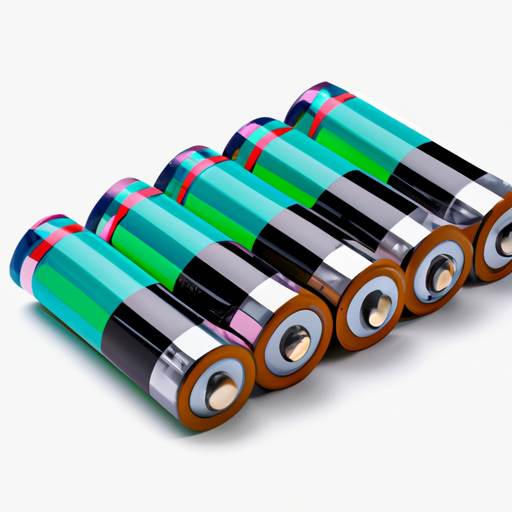
I. Introduction
A. Overview of CR2450 Batteries
CR2450 batteries are a type of lithium coin cell battery, widely recognized for their compact size and high energy density. Measuring 24mm in diameter and 5mm in thickness, these batteries typically provide a nominal voltage of 3 volts. They are commonly used in various electronic devices, including watches, calculators, medical devices, and remote controls, due to their long shelf life and reliability.
B. Importance of Battery Holders
Battery holders play a crucial role in the functionality of electronic devices. They not only secure the battery in place but also ensure proper electrical contact between the battery and the device. The design of battery holders must consider factors such as ease of battery replacement, compatibility with different battery types, and the overall aesthetics of the device. A well-designed battery holder enhances the user experience and contributes to the longevity of the device.
C. Purpose of the Article
This article aims to explore the production process of CR2450 battery holders, detailing the steps involved from material selection to quality control. Understanding this process is essential for manufacturers and consumers alike, as it highlights the complexities and considerations involved in producing a seemingly simple component.
II. Understanding CR2450 Battery Holders
A. Design and Structure
The design of CR2450 battery holders is critical for their functionality. Typically made from a combination of plastic and metal, these holders must provide both durability and conductivity. The plastic components often serve as the housing, while metal contacts ensure a reliable electrical connection.
1. Materials Used
Common materials for battery holders include polycarbonate and ABS plastic for the housing, and nickel-plated steel or brass for the contact points. The choice of materials is influenced by factors such as cost, weight, and electrical conductivity.
2. Types of Battery Holders
Battery holders can be categorized into several types, including snap-in holders, screw-mounted holders, and solderable holders. Each type has its specific applications and advantages, depending on the design requirements of the electronic device.
B. Key Features
1. Contact Points
The contact points in a battery holder are designed to ensure a secure connection with the battery terminals. These points must be engineered to withstand repeated insertions and removals without losing their conductive properties.
2. Retention Mechanisms
Retention mechanisms are essential for keeping the battery securely in place. Common designs include spring-loaded contacts and clips that hold the battery firmly, preventing it from rattling or disconnecting during use.
3. Size and Compatibility
The size of the battery holder must match the dimensions of the CR2450 battery, ensuring a snug fit. Additionally, compatibility with various electronic devices is crucial, as manufacturers often design holders that can accommodate multiple battery types.
III. The Production Process of CR2450 Battery Holders
A. Material Selection
The first step in the production process is material selection. Manufacturers must choose materials that meet the functional requirements of the battery holder while also considering cost-effectiveness and availability.
1. Types of Materials
As mentioned earlier, plastic and metal are the primary materials used in battery holders. The plastic components provide insulation and structural integrity, while the metal contacts ensure electrical conductivity.
2. Criteria for Material Selection
Key criteria for material selection include mechanical strength, thermal stability, and resistance to corrosion. Manufacturers often conduct tests to evaluate the performance of different materials under various conditions.
B. Design and Prototyping
Once materials are selected, the design phase begins. This involves creating detailed models of the battery holder using Computer-Aided Design (CAD) software.
1. CAD Modeling
CAD modeling allows designers to visualize the battery holder's structure and make necessary adjustments before moving to production. This step is crucial for identifying potential design flaws and ensuring that the holder meets all specifications.
2. Prototyping Techniques
Prototyping techniques such as 3D printing and CNC machining are employed to create physical models of the battery holder. These prototypes are tested for fit and functionality, providing valuable insights that inform the final design.
C. Manufacturing Techniques
The manufacturing of CR2450 battery holders involves several techniques, each with its advantages and disadvantages.
1. Injection Molding
Injection molding is one of the most common methods for producing plastic components of battery holders.
a. Process Overview
In this process, molten plastic is injected into a mold, where it cools and solidifies into the desired shape. This method is highly efficient for mass production, allowing for consistent quality and rapid output.
b. Advantages and Disadvantages
The primary advantage of injection molding is its ability to produce complex shapes with high precision. However, the initial setup costs for molds can be significant, making it less economical for small production runs.
2. Stamping and Forming
For the metal components, stamping and forming techniques are often used.
a. Process Overview
In stamping, sheets of metal are cut and shaped into the required forms using dies. This method is suitable for producing high volumes of metal parts quickly and accurately.
b. Applications in Battery Holder Production
Stamping is particularly useful for creating the contact points of battery holders, ensuring they maintain their shape and conductivity over time.
3. Assembly Processes
After the individual components are manufactured, they must be assembled into the final product.
a. Manual vs. Automated Assembly
Assembly can be done manually or through automated processes. Automated assembly lines are increasingly common, as they enhance efficiency and reduce labor costs.
b. Quality Control Measures
Quality control is essential during assembly to ensure that each battery holder meets the required specifications. This may involve visual inspections, dimensional checks, and functional testing.
D. Surface Treatment and Finishing
The final step in the production process involves surface treatment and finishing.
1. Coating Options
Surface treatments such as plating or painting are applied to enhance the durability and appearance of the battery holder. Nickel plating, for example, can improve corrosion resistance and conductivity.
2. Importance of Surface Treatment for Durability
Proper surface treatment is crucial for ensuring that the battery holder can withstand environmental factors such as humidity and temperature fluctuations, which can affect performance over time.
IV. Quality Control in Production
A. Importance of Quality Assurance
Quality assurance is a critical aspect of the production process, ensuring that each battery holder meets industry standards and customer expectations.
B. Testing Methods
Various testing methods are employed to assess the quality of battery holders.
1. Dimensional Checks
Dimensional checks verify that the battery holder's size and shape conform to specifications, ensuring a proper fit for the CR2450 battery.
2. Functional Testing
Functional testing assesses the electrical performance of the battery holder, ensuring that it provides a reliable connection with the battery.
3. Environmental Testing
Environmental testing evaluates the battery holder's performance under different conditions, such as extreme temperatures and humidity levels.
C. Compliance with Industry Standards
Manufacturers must comply with industry standards to ensure the safety and reliability of their products.
1. ISO Certifications
ISO certifications demonstrate that a manufacturer adheres to international quality management standards, providing assurance to customers regarding product quality.
2. Safety Regulations
Compliance with safety regulations is essential, particularly for battery holders used in medical devices and consumer electronics.
V. Challenges in the Production Process
A. Material Sourcing Issues
Sourcing high-quality materials can be challenging, particularly in times of supply chain disruptions. Manufacturers must establish reliable relationships with suppliers to ensure consistent quality.
B. Technological Advancements
Keeping up with technological advancements is crucial for manufacturers to remain competitive. This includes adopting new manufacturing techniques and materials that enhance product performance.
C. Market Demand Fluctuations
Market demand for CR2450 battery holders can fluctuate, impacting production volumes. Manufacturers must be agile in their production processes to respond to changing market conditions.
D. Environmental Considerations
Sustainability is becoming increasingly important in manufacturing. Companies must consider the environmental impact of their production processes and seek ways to minimize waste and energy consumption.
VI. Future Trends in Battery Holder Production
A. Innovations in Materials and Design
The future of battery holder production will likely see innovations in materials, such as the use of biodegradable plastics and advanced composites that offer improved performance and sustainability.
B. Automation and Industry 4.0
The integration of automation and Industry 4.0 technologies will enhance production efficiency, allowing manufacturers to produce battery holders with greater precision and speed.
C. Sustainability Practices in Production
Sustainability practices, such as recycling and waste reduction, will become increasingly important as manufacturers seek to minimize their environmental footprint.
VII. Conclusion
A. Recap of the CR2450 Battery Holder Production Process
The production process of CR2450 battery holders involves several critical steps, from material selection and design to manufacturing and quality control. Each stage plays a vital role in ensuring the final product meets the required specifications and performance standards.
B. The Significance of Quality and Innovation in the Industry
Quality and innovation are paramount in the battery holder manufacturing industry. As technology advances and consumer demands evolve, manufacturers must continuously improve their processes and products to remain competitive.
C. Final Thoughts on the Future of Battery Holder Manufacturing
The future of battery holder manufacturing looks promising, with advancements in materials, automation, and sustainability practices paving the way for more efficient and environmentally friendly production processes. As the demand for reliable and high-performance battery holders continues to grow, manufacturers must adapt and innovate to meet the challenges ahead.
VIII. References
A. Citing Relevant Literature and Sources
1. Battery University. (n.d.). "Battery Basics." Retrieved from [Battery University](https://batteryuniversity.com)
2. ISO. (n.d.). "ISO 9001:2015 - Quality Management Systems." Retrieved from [ISO](https://www.iso.org)
3. Electronics Weekly. (2021). "The Future of Battery Technology." Retrieved from [Electronics Weekly](https://www.electronicsweekly.com)
B. Additional Resources for Further Reading
1. "The Complete Guide to Battery Holders" - A comprehensive resource on battery holder design and applications.
2. "Advancements in Battery Technology" - An exploration of the latest trends and innovations in battery technology.
This blog post provides a detailed overview of the production process of CR2450 battery holders, highlighting the complexities and considerations involved in manufacturing this essential component.