The Production Process for Mainstream Export Products with Batteries
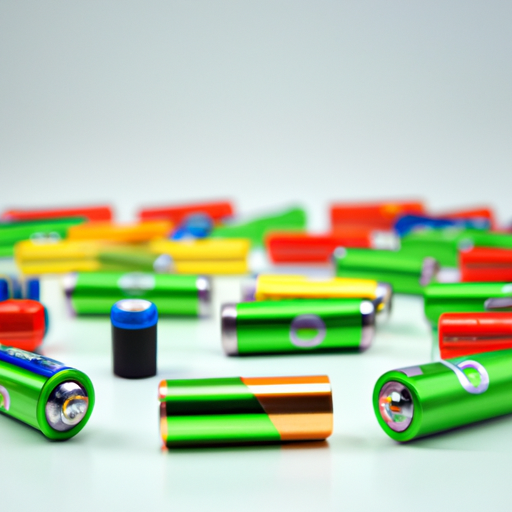
I. Introduction
In today's technology-driven world, batteries play a crucial role in powering a wide array of mainstream export products. From consumer electronics like smartphones and laptops to electric vehicles (EVs) and renewable energy storage systems, batteries are at the heart of modern innovation. As global demand for these products continues to rise, understanding the production process for battery-powered goods becomes increasingly important. This blog post will explore the various stages involved in the production of mainstream export products with batteries, highlighting the significance of raw materials, manufacturing processes, integration, logistics, challenges, and future trends.
II. Types of Mainstream Export Products with Batteries
The landscape of battery-powered products is diverse, encompassing several key categories:
A. Consumer Electronics
Smartphones, laptops, and tablets are ubiquitous in our daily lives. These devices rely on advanced battery technology to provide the portability and functionality that consumers expect. Lithium-ion batteries are the most common type used in these products due to their high energy density and lightweight characteristics.
B. Electric Vehicles (EVs)
The automotive industry is undergoing a significant transformation with the rise of electric vehicles. EVs utilize large battery packs, primarily lithium-ion, to power electric motors, offering a cleaner alternative to traditional gasoline-powered vehicles. The demand for EVs is surging as consumers and governments alike prioritize sustainability.
C. Renewable Energy Storage Systems
As the world shifts towards renewable energy sources, the need for efficient energy storage solutions has become paramount. Solar batteries, for instance, store excess energy generated from solar panels for later use, making them essential for residential and commercial applications.
D. Industrial Equipment
Power tools and machinery used in various industries also rely on battery technology. These products often utilize robust batteries designed to withstand demanding conditions while providing reliable performance.
III. Raw Materials Sourcing
A. Overview of Key Materials for Battery Production
The production of batteries requires several critical raw materials:
1. **Lithium**: A key component in lithium-ion batteries, lithium is primarily sourced from brine pools and hard rock mining.
2. **Cobalt**: Often used in conjunction with lithium to enhance battery performance, cobalt is mainly sourced from the Democratic Republic of Congo.
3. **Nickel**: This metal is essential for increasing energy density in batteries, and its demand is rising with the growth of EVs.
4. **Graphite**: Used as an anode material in lithium-ion batteries, graphite is sourced from both natural and synthetic processes.
B. Ethical Sourcing and Environmental Considerations
The extraction of these materials raises ethical and environmental concerns. Issues such as child labor in cobalt mining and the ecological impact of lithium extraction have prompted calls for more responsible sourcing practices. Companies are increasingly focusing on transparency in their supply chains to ensure ethical sourcing.
C. Global Supply Chain Dynamics
The global supply chain for battery materials is complex and often vulnerable to disruptions. Geopolitical tensions, trade policies, and environmental regulations can impact the availability and cost of raw materials, making it essential for manufacturers to develop resilient supply chains.
IV. Battery Manufacturing Process
A. Types of Batteries Used in Mainstream Products
The two most common types of batteries used in mainstream products are:
1. **Lithium-ion Batteries**: Known for their high energy density and long cycle life, these batteries are widely used in consumer electronics and EVs.
2. **Nickel-metal Hydride Batteries**: While less common than lithium-ion, these batteries are still used in some hybrid vehicles and consumer electronics.
B. Steps in Battery Production
The battery manufacturing process involves several key steps:
1. Material Preparation
Mining and Refining Raw Materials: The first step involves extracting and refining the necessary raw materials. This process can be resource-intensive and requires significant energy.
Chemical Processing: Once refined, the materials undergo chemical processing to create battery-grade compounds.
2. Cell Assembly
Electrode Fabrication: The next step involves creating the electrodes, which are critical components of the battery. This includes coating the electrodes with active materials.
Cell Formation and Electrolyte Filling: After fabricating the electrodes, they are assembled into cells, and the electrolyte is added to facilitate ion movement.
3. Quality Control and Testing
Quality control is paramount in battery production. Each battery undergoes rigorous testing to ensure safety, performance, and longevity. This includes checking for defects, capacity testing, and thermal stability assessments.
C. Innovations in Battery Technology
The battery industry is witnessing rapid innovations, including:
1. **Solid-State Batteries**: These batteries promise higher energy densities and improved safety by using solid electrolytes instead of liquid ones.
2. **Recycling and Sustainability Efforts**: As battery usage increases, so does the need for recycling. Companies are investing in technologies to recover valuable materials from used batteries, reducing environmental impact.
V. Integration into Final Products
A. Design Considerations for Battery Integration
Integrating batteries into final products requires careful design considerations. Manufacturers must ensure that the battery fits seamlessly within the product while maintaining safety and performance standards.
B. Assembly of Final Products
The assembly process varies depending on the product type:
1. **Consumer Electronics**: In devices like smartphones and laptops, batteries are often integrated into compact designs, requiring precision engineering.
2. **Electric Vehicles**: EV assembly involves larger battery packs, which must be securely mounted and connected to the vehicle's electrical system.
C. Quality Assurance and Testing of Final Products
Once assembled, final products undergo extensive quality assurance testing. This includes performance evaluations, safety checks, and compliance with regulatory standards to ensure that they meet consumer expectations.
VI. Export Logistics
A. Packaging and Transportation of Battery Products
Exporting battery-powered products involves specific packaging and transportation requirements. Batteries must be packaged to prevent damage and comply with international shipping regulations, particularly concerning hazardous materials.
B. Regulatory Compliance and Safety Standards
Manufacturers must adhere to various regulatory standards when exporting battery products. This includes compliance with safety standards set by organizations such as the International Electrotechnical Commission (IEC) and the United Nations (UN).
C. Market Trends and Demand for Battery-Powered Products
The demand for battery-powered products is on the rise, driven by trends such as the transition to electric vehicles, the growth of renewable energy, and the increasing reliance on portable electronics. Manufacturers must stay attuned to market trends to remain competitive.
VII. Challenges in the Production Process
A. Supply Chain Disruptions
The battery production process is susceptible to supply chain disruptions caused by geopolitical tensions, natural disasters, and pandemics. These disruptions can lead to delays and increased costs.
B. Environmental Impact and Sustainability Concerns
The environmental impact of battery production, from raw material extraction to manufacturing, raises sustainability concerns. Companies are under pressure to adopt greener practices and reduce their carbon footprint.
C. Technological Advancements and Competition
Rapid technological advancements in battery technology mean that manufacturers must continuously innovate to stay competitive. This includes investing in research and development to improve battery performance and reduce costs.
VIII. Future Trends in Battery Production
A. Advances in Battery Technology
The future of battery production is likely to be shaped by advances in technology, including the development of solid-state batteries and other next-generation solutions that promise higher efficiency and safety.
B. Shift Towards Sustainable Practices
As environmental concerns grow, the industry is shifting towards more sustainable practices, including the use of recycled materials and the development of eco-friendly manufacturing processes.
C. Impact of Global Policies on Battery Production and Export
Global policies aimed at reducing carbon emissions and promoting renewable energy will significantly impact battery production and export. Governments are likely to implement incentives for sustainable practices, influencing market dynamics.
IX. Conclusion
Batteries are integral to the production of mainstream export products, driving innovation and sustainability in various industries. As the demand for battery-powered goods continues to grow, understanding the production process becomes essential for manufacturers and consumers alike. The evolving landscape of battery production presents both challenges and opportunities, emphasizing the need for sustainable practices and ethical sourcing. As we move forward, it is crucial for stakeholders in the battery supply chain to prioritize sustainability and innovation, ensuring a cleaner and more efficient future for battery-powered products.
The Production Process for Mainstream Export Products with Batteries
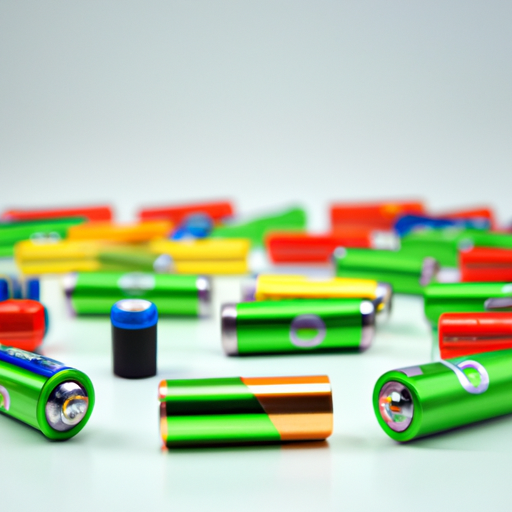
I. Introduction
In today's technology-driven world, batteries play a crucial role in powering a wide array of mainstream export products. From consumer electronics like smartphones and laptops to electric vehicles (EVs) and renewable energy storage systems, batteries are at the heart of modern innovation. As global demand for these products continues to rise, understanding the production process for battery-powered goods becomes increasingly important. This blog post will explore the various stages involved in the production of mainstream export products with batteries, highlighting the significance of raw materials, manufacturing processes, integration, logistics, challenges, and future trends.
II. Types of Mainstream Export Products with Batteries
The landscape of battery-powered products is diverse, encompassing several key categories:
A. Consumer Electronics
Smartphones, laptops, and tablets are ubiquitous in our daily lives. These devices rely on advanced battery technology to provide the portability and functionality that consumers expect. Lithium-ion batteries are the most common type used in these products due to their high energy density and lightweight characteristics.
B. Electric Vehicles (EVs)
The automotive industry is undergoing a significant transformation with the rise of electric vehicles. EVs utilize large battery packs, primarily lithium-ion, to power electric motors, offering a cleaner alternative to traditional gasoline-powered vehicles. The demand for EVs is surging as consumers and governments alike prioritize sustainability.
C. Renewable Energy Storage Systems
As the world shifts towards renewable energy sources, the need for efficient energy storage solutions has become paramount. Solar batteries, for instance, store excess energy generated from solar panels for later use, making them essential for residential and commercial applications.
D. Industrial Equipment
Power tools and machinery used in various industries also rely on battery technology. These products often utilize robust batteries designed to withstand demanding conditions while providing reliable performance.
III. Raw Materials Sourcing
A. Overview of Key Materials for Battery Production
The production of batteries requires several critical raw materials:
1. **Lithium**: A key component in lithium-ion batteries, lithium is primarily sourced from brine pools and hard rock mining.
2. **Cobalt**: Often used in conjunction with lithium to enhance battery performance, cobalt is mainly sourced from the Democratic Republic of Congo.
3. **Nickel**: This metal is essential for increasing energy density in batteries, and its demand is rising with the growth of EVs.
4. **Graphite**: Used as an anode material in lithium-ion batteries, graphite is sourced from both natural and synthetic processes.
B. Ethical Sourcing and Environmental Considerations
The extraction of these materials raises ethical and environmental concerns. Issues such as child labor in cobalt mining and the ecological impact of lithium extraction have prompted calls for more responsible sourcing practices. Companies are increasingly focusing on transparency in their supply chains to ensure ethical sourcing.
C. Global Supply Chain Dynamics
The global supply chain for battery materials is complex and often vulnerable to disruptions. Geopolitical tensions, trade policies, and environmental regulations can impact the availability and cost of raw materials, making it essential for manufacturers to develop resilient supply chains.
IV. Battery Manufacturing Process
A. Types of Batteries Used in Mainstream Products
The two most common types of batteries used in mainstream products are:
1. **Lithium-ion Batteries**: Known for their high energy density and long cycle life, these batteries are widely used in consumer electronics and EVs.
2. **Nickel-metal Hydride Batteries**: While less common than lithium-ion, these batteries are still used in some hybrid vehicles and consumer electronics.
B. Steps in Battery Production
The battery manufacturing process involves several key steps:
1. Material Preparation
Mining and Refining Raw Materials: The first step involves extracting and refining the necessary raw materials. This process can be resource-intensive and requires significant energy.
Chemical Processing: Once refined, the materials undergo chemical processing to create battery-grade compounds.
2. Cell Assembly
Electrode Fabrication: The next step involves creating the electrodes, which are critical components of the battery. This includes coating the electrodes with active materials.
Cell Formation and Electrolyte Filling: After fabricating the electrodes, they are assembled into cells, and the electrolyte is added to facilitate ion movement.
3. Quality Control and Testing
Quality control is paramount in battery production. Each battery undergoes rigorous testing to ensure safety, performance, and longevity. This includes checking for defects, capacity testing, and thermal stability assessments.
C. Innovations in Battery Technology
The battery industry is witnessing rapid innovations, including:
1. **Solid-State Batteries**: These batteries promise higher energy densities and improved safety by using solid electrolytes instead of liquid ones.
2. **Recycling and Sustainability Efforts**: As battery usage increases, so does the need for recycling. Companies are investing in technologies to recover valuable materials from used batteries, reducing environmental impact.
V. Integration into Final Products
A. Design Considerations for Battery Integration
Integrating batteries into final products requires careful design considerations. Manufacturers must ensure that the battery fits seamlessly within the product while maintaining safety and performance standards.
B. Assembly of Final Products
The assembly process varies depending on the product type:
1. **Consumer Electronics**: In devices like smartphones and laptops, batteries are often integrated into compact designs, requiring precision engineering.
2. **Electric Vehicles**: EV assembly involves larger battery packs, which must be securely mounted and connected to the vehicle's electrical system.
C. Quality Assurance and Testing of Final Products
Once assembled, final products undergo extensive quality assurance testing. This includes performance evaluations, safety checks, and compliance with regulatory standards to ensure that they meet consumer expectations.
VI. Export Logistics
A. Packaging and Transportation of Battery Products
Exporting battery-powered products involves specific packaging and transportation requirements. Batteries must be packaged to prevent damage and comply with international shipping regulations, particularly concerning hazardous materials.
B. Regulatory Compliance and Safety Standards
Manufacturers must adhere to various regulatory standards when exporting battery products. This includes compliance with safety standards set by organizations such as the International Electrotechnical Commission (IEC) and the United Nations (UN).
C. Market Trends and Demand for Battery-Powered Products
The demand for battery-powered products is on the rise, driven by trends such as the transition to electric vehicles, the growth of renewable energy, and the increasing reliance on portable electronics. Manufacturers must stay attuned to market trends to remain competitive.
VII. Challenges in the Production Process
A. Supply Chain Disruptions
The battery production process is susceptible to supply chain disruptions caused by geopolitical tensions, natural disasters, and pandemics. These disruptions can lead to delays and increased costs.
B. Environmental Impact and Sustainability Concerns
The environmental impact of battery production, from raw material extraction to manufacturing, raises sustainability concerns. Companies are under pressure to adopt greener practices and reduce their carbon footprint.
C. Technological Advancements and Competition
Rapid technological advancements in battery technology mean that manufacturers must continuously innovate to stay competitive. This includes investing in research and development to improve battery performance and reduce costs.
VIII. Future Trends in Battery Production
A. Advances in Battery Technology
The future of battery production is likely to be shaped by advances in technology, including the development of solid-state batteries and other next-generation solutions that promise higher efficiency and safety.
B. Shift Towards Sustainable Practices
As environmental concerns grow, the industry is shifting towards more sustainable practices, including the use of recycled materials and the development of eco-friendly manufacturing processes.
C. Impact of Global Policies on Battery Production and Export
Global policies aimed at reducing carbon emissions and promoting renewable energy will significantly impact battery production and export. Governments are likely to implement incentives for sustainable practices, influencing market dynamics.
IX. Conclusion
Batteries are integral to the production of mainstream export products, driving innovation and sustainability in various industries. As the demand for battery-powered goods continues to grow, understanding the production process becomes essential for manufacturers and consumers alike. The evolving landscape of battery production presents both challenges and opportunities, emphasizing the need for sustainable practices and ethical sourcing. As we move forward, it is crucial for stakeholders in the battery supply chain to prioritize sustainability and innovation, ensuring a cleaner and more efficient future for battery-powered products.