What is the Production Process of Mainstream BYD Battery Products?
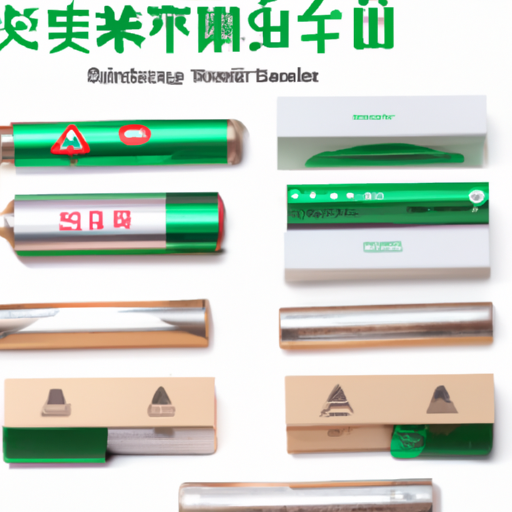
I. Introduction
In the rapidly evolving landscape of electric vehicles (EVs) and renewable energy, battery technology plays a pivotal role. BYD, short for Build Your Dreams, has emerged as a leading manufacturer in this sector, renowned for its innovative battery solutions. Founded in 1995, BYD has grown from a small battery manufacturer to a global powerhouse, producing batteries for various applications, including electric vehicles, energy storage systems, and consumer electronics. This article aims to explore the intricate production process of BYD's mainstream battery products, shedding light on the technology, sourcing, manufacturing, and sustainability efforts that define their operations.
II. Understanding BYD's Battery Technology
A. Types of Batteries Produced by BYD
BYD specializes in two primary types of lithium-ion batteries: Lithium Iron Phosphate (LiFePO4) and Lithium Nickel Manganese Cobalt (NMC) batteries.
1. **Lithium Iron Phosphate (LiFePO4) Batteries**: Known for their thermal stability and safety, LiFePO4 batteries are widely used in electric buses and other heavy-duty applications. They offer a longer cycle life and are less prone to overheating, making them a preferred choice for large-scale energy storage.
2. **Lithium Nickel Manganese Cobalt (NMC) Batteries**: These batteries are designed for high energy density and are commonly used in passenger electric vehicles. NMC batteries provide a balance between performance, cost, and safety, making them suitable for a wide range of applications.
B. Applications of BYD Batteries
BYD batteries find applications across various sectors:
1. **Electric Vehicles**: BYD is one of the largest manufacturers of electric buses and cars, utilizing its advanced battery technology to power its vehicles.
2. **Energy Storage Systems**: BYD's batteries are integral to renewable energy storage solutions, enabling the efficient use of solar and wind energy.
3. **Consumer Electronics**: The company also produces batteries for smartphones, laptops, and other portable devices, showcasing the versatility of its technology.
III. Raw Material Sourcing
A. Importance of Raw Materials in Battery Production
The quality and sustainability of raw materials are crucial in battery production. The performance, safety, and environmental impact of batteries are directly linked to the materials used in their manufacture.
B. Key Materials Used in BYD Batteries
1. **Lithium**: A critical component for energy storage, lithium is sourced from various global suppliers, with a focus on sustainable practices.
2. **Cobalt**: While cobalt enhances battery performance, its sourcing has raised ethical concerns. BYD is committed to responsible sourcing to mitigate these issues.
3. **Nickel**: Nickel is essential for increasing energy density, particularly in NMC batteries.
4. **Phosphate**: Used in LiFePO4 batteries, phosphate contributes to safety and stability.
C. BYD's Approach to Sustainable Sourcing
BYD emphasizes sustainable sourcing through partnerships with suppliers who adhere to ethical practices. The company also invests in recycling initiatives to reclaim valuable materials from used batteries, reducing the need for new raw materials and minimizing environmental impact.
IV. Battery Cell Manufacturing Process
A. Overview of the Manufacturing Process
The production of BYD batteries involves a series of meticulously controlled processes to ensure high quality and performance.
B. Key Stages in Battery Cell Production
1. **Electrode Preparation**:
- **Mixing Active Materials**: The process begins with the precise mixing of active materials, conductive agents, and binders to create a slurry.
- **Coating and Drying**: The slurry is then coated onto metal foils (copper for anodes and aluminum for cathodes) and dried to remove solvents.
2. **Cell Assembly**:
- **Stacking or Winding Electrodes**: Depending on the design, electrodes are either stacked or wound to form the cell structure.
- **Inserting Separators**: A separator is inserted to prevent short circuits while allowing lithium ions to pass through.
- **Electrolyte Filling**: The cell is filled with electrolyte, which facilitates ion movement during charging and discharging.
3. **Formation and Aging**:
- **Initial Charging Cycles**: The cells undergo initial charging cycles to form a stable solid electrolyte interphase (SEI) layer, crucial for battery performance.
- **Quality Control Measures**: Rigorous testing is conducted to ensure that each cell meets safety and performance standards.
V. Battery Pack Assembly
A. Importance of Battery Pack Design
The design of the battery pack is critical for the overall performance and safety of the battery system. It must accommodate thermal management, electrical connections, and structural integrity.
B. Stages of Battery Pack Assembly
1. **Module Assembly**:
- **Grouping Cells into Modules**: Cells are grouped into modules, which are the building blocks of the battery pack.
- **Thermal Management Integration**: Effective thermal management systems are integrated to maintain optimal operating temperatures.
2. **Pack Assembly**:
- **Connecting Modules**: Modules are connected to form the complete battery pack, ensuring proper electrical connections.
- **Incorporating Battery Management Systems (BMS)**: A BMS is integrated to monitor and manage the performance of the battery pack, ensuring safety and efficiency.
C. Testing and Quality Assurance
1. **Performance Testing**: Each battery pack undergoes rigorous performance testing to ensure it meets specifications for energy output and efficiency.
2. **Safety Testing**: Safety tests, including thermal runaway and short-circuit tests, are conducted to ensure the battery pack can withstand extreme conditions.
VI. Research and Development
A. BYD's Commitment to Innovation
BYD invests heavily in research and development to stay at the forefront of battery technology. The company recognizes that continuous innovation is essential for improving performance and sustainability.
B. Role of R&D in Improving Battery Technology
1. **Enhancements in Energy Density**: Ongoing research aims to increase the energy density of batteries, allowing for longer ranges in electric vehicles.
2. **Advances in Charging Speed and Cycle Life**: BYD is focused on developing faster charging solutions and extending the cycle life of batteries, making them more convenient for consumers.
C. Collaboration with Academic and Industry Partners
BYD collaborates with universities and industry leaders to drive innovation. These partnerships facilitate knowledge exchange and accelerate the development of cutting-edge technologies.
VII. Environmental Considerations
A. BYD's Sustainability Initiatives
BYD is committed to sustainability, implementing initiatives to reduce its environmental footprint throughout the battery production process.
B. Waste Management and Recycling Processes
The company has established waste management protocols to minimize waste generation and promote recycling. Used batteries are collected and processed to recover valuable materials, reducing the need for new raw materials.
C. Life Cycle Assessment of BYD Batteries
BYD conducts life cycle assessments to evaluate the environmental impact of its batteries from raw material extraction to end-of-life disposal. This holistic approach helps the company identify areas for improvement and enhance sustainability.
VIII. Conclusion
In summary, the production process of BYD's mainstream battery products is a complex and highly regulated operation that emphasizes quality, safety, and sustainability. From raw material sourcing to advanced manufacturing techniques, BYD is committed to delivering high-performance batteries that power the future of electric vehicles and renewable energy solutions. As the demand for sustainable energy solutions continues to grow, BYD's innovative approach positions it as a key player in the battery industry, paving the way for a greener and more sustainable future. The company's ongoing commitment to research and development, coupled with its focus on environmental considerations, ensures that BYD will remain at the forefront of battery technology for years to come.
What is the Production Process of Mainstream BYD Battery Products?
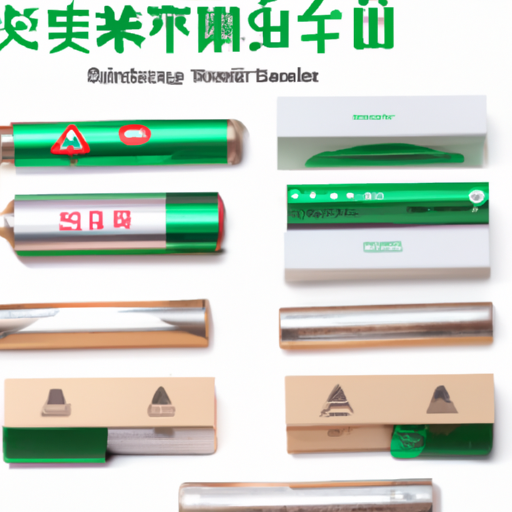
I. Introduction
In the rapidly evolving landscape of electric vehicles (EVs) and renewable energy, battery technology plays a pivotal role. BYD, short for Build Your Dreams, has emerged as a leading manufacturer in this sector, renowned for its innovative battery solutions. Founded in 1995, BYD has grown from a small battery manufacturer to a global powerhouse, producing batteries for various applications, including electric vehicles, energy storage systems, and consumer electronics. This article aims to explore the intricate production process of BYD's mainstream battery products, shedding light on the technology, sourcing, manufacturing, and sustainability efforts that define their operations.
II. Understanding BYD's Battery Technology
A. Types of Batteries Produced by BYD
BYD specializes in two primary types of lithium-ion batteries: Lithium Iron Phosphate (LiFePO4) and Lithium Nickel Manganese Cobalt (NMC) batteries.
1. **Lithium Iron Phosphate (LiFePO4) Batteries**: Known for their thermal stability and safety, LiFePO4 batteries are widely used in electric buses and other heavy-duty applications. They offer a longer cycle life and are less prone to overheating, making them a preferred choice for large-scale energy storage.
2. **Lithium Nickel Manganese Cobalt (NMC) Batteries**: These batteries are designed for high energy density and are commonly used in passenger electric vehicles. NMC batteries provide a balance between performance, cost, and safety, making them suitable for a wide range of applications.
B. Applications of BYD Batteries
BYD batteries find applications across various sectors:
1. **Electric Vehicles**: BYD is one of the largest manufacturers of electric buses and cars, utilizing its advanced battery technology to power its vehicles.
2. **Energy Storage Systems**: BYD's batteries are integral to renewable energy storage solutions, enabling the efficient use of solar and wind energy.
3. **Consumer Electronics**: The company also produces batteries for smartphones, laptops, and other portable devices, showcasing the versatility of its technology.
III. Raw Material Sourcing
A. Importance of Raw Materials in Battery Production
The quality and sustainability of raw materials are crucial in battery production. The performance, safety, and environmental impact of batteries are directly linked to the materials used in their manufacture.
B. Key Materials Used in BYD Batteries
1. **Lithium**: A critical component for energy storage, lithium is sourced from various global suppliers, with a focus on sustainable practices.
2. **Cobalt**: While cobalt enhances battery performance, its sourcing has raised ethical concerns. BYD is committed to responsible sourcing to mitigate these issues.
3. **Nickel**: Nickel is essential for increasing energy density, particularly in NMC batteries.
4. **Phosphate**: Used in LiFePO4 batteries, phosphate contributes to safety and stability.
C. BYD's Approach to Sustainable Sourcing
BYD emphasizes sustainable sourcing through partnerships with suppliers who adhere to ethical practices. The company also invests in recycling initiatives to reclaim valuable materials from used batteries, reducing the need for new raw materials and minimizing environmental impact.
IV. Battery Cell Manufacturing Process
A. Overview of the Manufacturing Process
The production of BYD batteries involves a series of meticulously controlled processes to ensure high quality and performance.
B. Key Stages in Battery Cell Production
1. **Electrode Preparation**:
- **Mixing Active Materials**: The process begins with the precise mixing of active materials, conductive agents, and binders to create a slurry.
- **Coating and Drying**: The slurry is then coated onto metal foils (copper for anodes and aluminum for cathodes) and dried to remove solvents.
2. **Cell Assembly**:
- **Stacking or Winding Electrodes**: Depending on the design, electrodes are either stacked or wound to form the cell structure.
- **Inserting Separators**: A separator is inserted to prevent short circuits while allowing lithium ions to pass through.
- **Electrolyte Filling**: The cell is filled with electrolyte, which facilitates ion movement during charging and discharging.
3. **Formation and Aging**:
- **Initial Charging Cycles**: The cells undergo initial charging cycles to form a stable solid electrolyte interphase (SEI) layer, crucial for battery performance.
- **Quality Control Measures**: Rigorous testing is conducted to ensure that each cell meets safety and performance standards.
V. Battery Pack Assembly
A. Importance of Battery Pack Design
The design of the battery pack is critical for the overall performance and safety of the battery system. It must accommodate thermal management, electrical connections, and structural integrity.
B. Stages of Battery Pack Assembly
1. **Module Assembly**:
- **Grouping Cells into Modules**: Cells are grouped into modules, which are the building blocks of the battery pack.
- **Thermal Management Integration**: Effective thermal management systems are integrated to maintain optimal operating temperatures.
2. **Pack Assembly**:
- **Connecting Modules**: Modules are connected to form the complete battery pack, ensuring proper electrical connections.
- **Incorporating Battery Management Systems (BMS)**: A BMS is integrated to monitor and manage the performance of the battery pack, ensuring safety and efficiency.
C. Testing and Quality Assurance
1. **Performance Testing**: Each battery pack undergoes rigorous performance testing to ensure it meets specifications for energy output and efficiency.
2. **Safety Testing**: Safety tests, including thermal runaway and short-circuit tests, are conducted to ensure the battery pack can withstand extreme conditions.
VI. Research and Development
A. BYD's Commitment to Innovation
BYD invests heavily in research and development to stay at the forefront of battery technology. The company recognizes that continuous innovation is essential for improving performance and sustainability.
B. Role of R&D in Improving Battery Technology
1. **Enhancements in Energy Density**: Ongoing research aims to increase the energy density of batteries, allowing for longer ranges in electric vehicles.
2. **Advances in Charging Speed and Cycle Life**: BYD is focused on developing faster charging solutions and extending the cycle life of batteries, making them more convenient for consumers.
C. Collaboration with Academic and Industry Partners
BYD collaborates with universities and industry leaders to drive innovation. These partnerships facilitate knowledge exchange and accelerate the development of cutting-edge technologies.
VII. Environmental Considerations
A. BYD's Sustainability Initiatives
BYD is committed to sustainability, implementing initiatives to reduce its environmental footprint throughout the battery production process.
B. Waste Management and Recycling Processes
The company has established waste management protocols to minimize waste generation and promote recycling. Used batteries are collected and processed to recover valuable materials, reducing the need for new raw materials.
C. Life Cycle Assessment of BYD Batteries
BYD conducts life cycle assessments to evaluate the environmental impact of its batteries from raw material extraction to end-of-life disposal. This holistic approach helps the company identify areas for improvement and enhance sustainability.
VIII. Conclusion
In summary, the production process of BYD's mainstream battery products is a complex and highly regulated operation that emphasizes quality, safety, and sustainability. From raw material sourcing to advanced manufacturing techniques, BYD is committed to delivering high-performance batteries that power the future of electric vehicles and renewable energy solutions. As the demand for sustainable energy solutions continues to grow, BYD's innovative approach positions it as a key player in the battery industry, paving the way for a greener and more sustainable future. The company's ongoing commitment to research and development, coupled with its focus on environmental considerations, ensures that BYD will remain at the forefront of battery technology for years to come.